W jaki sposób producent obróbki metali decyduje się na zastosowanie technologii wytwarzania lub tłoczenia?
Producent warsztatu obróbki metali nie myśli o odrzuceniu klienta, ale zanim klient złoży realną prośbę, nigdy nie wiadomo, czego potrzebuje, trzeba być przygotowanym na wszystko. Więcej narzędzi w zestawie narzędzi może zwiększyć zdolność producenta do obsługi wymaganej ilości, czasu i złożoności części. Producenci z cechowanie możliwości mogą dobrze obsłużyć prawie każde wymagania.
Po zakończeniu projektowania pojawia się kolejna trudność: Którą ścieżkę procesu stosujesz? Jakie instrukcje należy wykonać na wykrawarce, głowicy laserowej lub giętarce?
Tłoczenie czy produkcja? Jak podejmujesz decyzję? ACE Stamping & Machine Co., Racine, Wisconsin, General Stamping and Metal Factory (GSM), South Bend, Indiana; Kapco Metal Stamping z Grafton w stanie Wisconsin również podzieliło się swoimi poglądami i metodami dotyczącymi tego problemu.
James Haarsma, wiceprezes ACE Stamping and Machinery, powiedział: „Jak określić, którą trasę wybrać, jest jednym z największych wyzwań, przed którymi stoimy. To jest coś, z czym walczę każdego dnia”.
Prezes i dyrektor generalny GSM John Axelberg (John Axelberg) powiedział: „Wybierając metodę produkcji dla określonej części, weźmiemy pod uwagę cykl dostawy produktu i całkowitą wydajność całego cyklu życia produktu i spróbujemy zaproponować opcję najniższego kosztu. "
Mike Kenny, wiceprezes Kapco, powiedział: „W przypadku każdej części bierzemy pod uwagę roczną produkcję, geometrię, wymiary, cechy, tolerancje, materiały, tonaż i wielkość wymagań sprzętowych oraz zwrot z inwestycji w narzędzia klienta jako kluczowe punkty decyzyjne, które wpływają na określony proces. Wybór produkcji, tłoczenia lub ich kombinacji jest wynikiem określenia najbardziej wydajnego procesu do produkcji spójnych, wolnych od wad części przy najniższych kosztach całkowitych”.
1. Wydatki
Koszt to kluczowy punkt, w którym współdziałają wszystkie inne czynniki. Producenci wykorzystują zalety każdego procesu, aby osiągnąć opłacalność.
Kenny przytacza zdolność technologii stemplowania do łączenia wielu operacji w maszynie do stemplowania jako sposobu na rozszerzenie skali. „Jeśli istnieje możliwość połączenia innych operacji w procesie tłoczenia, takich jak mocowanie, gwintowanie, wytłaczanie, tłoczenie lub znakowanie części, wówczas obniżenie kosztów części zwykle zrekompensuje inwestycję w narzędzia do tłoczenia i pomoże w podjęciu decyzji”. Powiedział .
Dodał, że stemplowanie może być zautomatyzowane i wymaga mniej pracy dla każdej części niż inne operacje (takie jak ręczne giętarki).
2. Objętość części
Częściowa podróż jest oczywiście jednym z kluczowych czynników decydujących o wyborze ścieżki. Haarsma powiedział: „Wielkość obrotu jest zwykle Twoim pierwszym wskaźnikiem. Dlatego stosujemy próg 6,000 6,000 rocznie. Jeśli roczna partia części wynosi 15,000 XNUMX lub więcej, zwykle chcemy ją stemplować”. Taki jest czas maszyny. W ramach decyzji, tak samo jak czas dostawy. „W tempie XNUMX XNUMX części rocznie cały czas mojej maszyny będzie pochłaniany przez wieżyczki lub lasery. Nasz czas dostawy również będzie zbyt długi”.
Haarsma ograniczył punkt przerwania i powiedział, że to tylko praktyczna zasada. „W zależności od innych czynników możemy wydrukować tylko 3,000 części rocznie”.
Kenny mocno przestrzega ścisłych zasad ilościowych. „Wstępne określenie liczby, cyklu życia i dynamiki projektowania poprowadzi zespół do przodu, ale nie ma jasnej reguły”. Kiedy został przyciśnięty, wymienił krytyczną wartość. Powiedział: „Ogólnie rzecz biorąc, części o rocznej produkcji 5,000 XNUMX lub większej będą szukały biznesu w zakresie tłoczenia”.
Axelberg w ogóle nie wskazał wartości krytycznej. „Nigdy nie narysowaliśmy linii na piasku. Postaramy się jak najlepiej zrozumieć potrzeby i cele klienta. Jeśli wybór nie będzie jasny, zaproponujemy różne opcje. Nie ma ustalonej liczby, która dotyczy wszystkich obszarów, ponieważ każda część jest niepowtarzalna. To właśnie sprawia, że ten biznes jest tak interesujący!"
3. Harmonogram
Czas realizacji i rozwój produktu mogą powodować cykl życia części od początku produkcji do końca tłoczenia.
Axelberg wyjaśnił, w jaki sposób rozkład jazdy klienta stał się główną siłą napędową. Powiedział: „Dużo zależy od tego, kiedy klient potrzebuje części”. „Dla jednego z naszych dużych klientów przetworzyliśmy 20,000 XNUMX wielkogabarytowych części za pomocą laserów i giętarek w sześć tygodni”.
Axelberg dodał, że ponieważ praca ta wymaga bardzo dużego rocznego wolumenu przetwarzania, GSM stosuje długoterminowe, rygorystyczne narzędzia, które mogą przejąć projekt, gdy jest gotowy. „Następnie w ciągu 12 tygodni części są przekształcane w części tłoczone. Dlatego zaczyna się od miękkich narzędzi, a kończy na twardych narzędziach. Będziemy to robić regularnie”.
Axelberg powiedział, że w pewnym stopniu technologia laserowa napędza zapotrzebowanie na to dwutorowe podejście. „Myślę, że wielu producentów oryginalnego sprzętu przyzwyczaiło się do szybkiego reagowania zakładów produkujących lasery i ich zdolności do szybkiego wytwarzania prawie każdego produktu”. W rezultacie, gdy produkt jest jeszcze w fazie testów, klienci mogą nie zacząć rozważać używania twardych narzędzi . W innych przypadkach należy opracować ostateczny projekt części. W takim przypadku GSM rozpocznie się od cięcie laserowe/ gięcie formowania, a następnie przekształcić się w narzędzie do tłoczenia.
Axelberg powiedział, że kolejnym powodem, dla którego klienci mogą nie być w stanie rozpocząć pracy w odpowiednim czasie, aby pomieścić matryce, jest charakter ich sektorów przemysłu. Energia słoneczna to nieprzewidywalna branża. Projekty mogą być bardzo duże i zazwyczaj są to złożone transakcje ze względu na złożoność finansowania i licencjonowania. Termin oddania projektu do użytku został wcześniej określony. Ostatniego dnia wszystkie inne szczegóły mogą zostać naruszone. Dlatego w przypadku wielu z tych zawodów, kiedy są już zdeterminowane i dobrze prosperują, musimy odejść. To dużo części. "
Axelberg powiedział, że wprowadzenie laserów światłowodowych o dużej mocy miało duży wpływ na obliczenia niezależne od rodzaju materiału. Około pięć lat temu firma GSM budowała wykrojniki i wykrojniki do obsługi wyciętych półfabrykatów w swoich prasach. Pomimo wszystkich operacji ręcznych, proces jest nadal szybszy niż cięcie części laserem. „Będziemy obrabiać prostokątne części z kwadratowymi rogami na stemplach CNC, ponieważ jest to szybsze niż cięcie laserowe. Już nie. Teraz rezerwujemy stemple dla tych części z możliwością 3D, których nie można utworzyć na laserach. Ponieważ te stemple nie mogą zacząć zbliżać się do profilowania prędkość lasera światłowodowego."
4. Rozmiar części
Kenny omówił inny czynnik: rozmiar części. Powiedział, że duża część prawdopodobnie zmusi operację do przejścia na produkcję, a nie na tłoczenie. „Dzieje się tak, ponieważ koszt narzędzia wzrasta z każdą przyrostową operacją w narzędziu, a kompletne narzędzie może wymagać więcej nieruchomości niż dostępna jest prasa drukarska”.
Kenny zwrócił uwagę, że mniejsze części mają niższe koszty form, więc zwrot z inwestycji jest krótszy. „Duże części mogą wymagać większej rocznej liczby wydruków. Alternatywnie możemy rozważyć wiele procesów, takich jak cięcie laserowe półfabrykatu, a następnie ręczne przenoszenie go do formy formującej lub wykrawanie w formie, a następnie formowanie na giętarce”.
Haarsma powiedział, że ograniczenie rozmiaru zależy od czasu formowania matryc, ponieważ największe łoże do tłoczenia w firmie ma 8 stóp długości. „Więc dla nas, jeśli element jest duży i ma pistolety do wybijania, odciążania i natryskiwania, będziesz potrzebować automatycznego systemu pras — 2,000 ton, pras jeden do drugiego z powodu progresywnej selekcji. Za długo. Dlatego , w przypadku większych części o wielu cechach formowania, rozmiar jest czynnikiem ograniczającym tłoczenie”.
5. Kształty, kontury, kształty geometryczne, cechy
Kenny powiedział, że w wielu przypadkach geometria części, cechy, tolerancje oraz wymagane specyfikacje dotyczące tonażu i wymiarów są głównymi powodami, dla których Kapco wybiera tłoczenie, a nie produkcję.
Powiedział: „W prasie serwo mogą występować pewne cechy, takie jak otwory, zagłębienia, przetłoczenia i żebra lub tolerancje, które są korzystniejsze w prasie serwo, co może skłaniać do rozważenia ich tłoczenia”. „Rozmiar otwór i jego położenie względem krawędzi mogą pomóc w wyborze tłoczenia lub produkcji."
Axelberg powiedział, że niektóre projekty części nie mają innego wyjścia, jak tworzyć matryce. Giętarki przeznaczone są do gięcia, a nie formowania. Dlatego wyprodukowaliśmy tylko setki wykrojników. "
Haarsma zgodził się. „Na przykład stemplowanie jest jedynym procesem, który może utworzyć okrąg”. Dodał, że ze względu na ich złożoność niektóre wysokiej jakości części będą działały na prasie rewolwerowej.
„Mam niektóre części z wieloma perforowanymi otworami, a roczna produkcja jest bardzo wysoka. Pracujemy na prasie rewolwerowej. To dlatego, że wiele rzeczy dzieje się w częściach. Jeśli umieścimy je w progresywnym narzędziu, będzie to Za długo. Klienci nie zapłacą za narzędzie o wartości 300,000 XNUMX USD, chyba że jest to duża liczba.
„Skończyło się na tym, że uruchomiliśmy je na prasach rewolwerowych i wykrawarkach, ponieważ można w nich umieścić wiele form i wykonać wszystkie cięcia naraz. Następnie wprowadzasz je do operacji pomocniczych, aby je uformować, tak jak zagięcie pod kątem 90 stopni. „Haarsma powiedział.
Haarsma powiedział, że rozmiar decyduje o tym, że gdy cecha kształtu jest duża, część powinna być wykrawana na stemplu. „Jeśli jest okrągły, membranowy lub coś w tym rodzaju, jeśli jest większy niż 4 cale, nie można wybić otworów w prasie rewolwerowej, ponieważ ma ten sam rozmiar co uchwyt narzędziowy”. Dlatego tylko ze względu na geometrię części musimy ją przebić. "
6. Tolerancja
Haarsma powiedział, że innym czynnikiem decydującym o twardej formie jest tolerancja, której nie można utrzymać zarówno w stemplach rewolwerowych, jak i prasach wykrojnikowych. „Miesięcznie napotykaliśmy 200 części. Stemplowaliśmy je, ponieważ mieliśmy 300 otworów, które były blisko siebie z tolerancją +0/-1 i położeniem +0/-2”.
Kenny powiedział, że stemplowanie może poprawić kontrolę tolerancji i zwiększyć powtarzalność, ponieważ narzędzie może wykonać zadanie. „Można dodać elementy sterujące i czujniki, aby lepiej kontrolować proces”.
7. Obróbka powierzchni, jakość krawędzi
Producenci twierdzą, że preferencje klientów dotyczące konkretnych wykończeń mogą wskazywać w jednym kierunku.
„Warunki krawędzi, od tłoczenia do cięcia laserowego, są zupełnie inne”, powiedział Axelberg. „W zależności od rodzaju formowanej listwy, małe pęknięcia mogą być bardziej prawdopodobne na krawędzi skrawającej.
Halsma przedstawia inny punkt widzenia. „Czasami klienci nie chcą krawędzi wycinanych laserowo. Wolą wytłoczone krawędzie z pęknięciami i przegięciami, dzięki czemu można wyczyścić 70% materiału. Wtedy zaczynają się pojawiać przełomy i przejścia, ale można je ogratować. Za pomocą Krawędź cięcia laserowego, w zależności od grubości części, zaczniesz widzieć częstotliwość wiązki. Wpłynie to na wykończenie boku."
Kenny dodał: „Za pomocą serwoprasy można poprawić stopień separacji”.
8. Rodzaj materiału
Haarsma powiedział, że chociaż rodzaj materiału tworzącego komponent jest czynnikiem, wraz z pojawieniem się technologii lasera światłowodowego jego liczba nie jest tak wysoka jak wcześniej. „Prasowaliśmy tytan, złoto i mosiądz. W przeszłości byliśmy bardzo ograniczeni. Nie mogliśmy używać laserów CO2 do cięcia tytanu, mosiądzu ani żadnego czerwonego metalu jako materiałów odblaskowych. Półtora roku temu kupiliśmy światłowody, które mogą przenikać te materiały odblaskowe. Laser."
9. Wykorzystanie materiału
Axelberg powiedział, że kolejnym kluczowym wyznacznikiem jest wykorzystanie surowców. „Geometria niektórych części może pozostawiać dużo odpadów w tłocznikach, ale po zagnieżdżeniu z innymi częściami w laserze prawie nie ma odpadów”. Ogólnie rzecz biorąc, oszczędność kosztów materiałów może uzasadniać wyższe koszty przetwarzania. Axelberg dodał: „Ten punkt zwrotny zmienia się w zależności od ceny stali.
„Na przykład części są wykonane z metalu klasy 50 z ocynkowaniem nr 8. Ponieważ produkcja zaczyna się wspinać, mamy nadzieję, że przejdziemy do pełnej progresywnej formy. Niestety, ze względu na wykorzystanie materiału w porównaniu z obróbką laserową Słaba, więc okres zwrotu formy wynosi około 21/2 roku. Dlatego zaproponowaliśmy kompromis. Zbudowaliśmy dwuwymiarową formę do uruchomienia cewki, która odpowiadała wydajności materiału lasera i znacznie zwiększała wydajność. Operacja formowania jest nadal zakończona w dwustopniowej formie formującej innej prasy.”
Kenny powiedział, że odkrył, że proces tłoczenia ma lepsze wykorzystanie materiału i niższe koszty procesu niż proces produkcyjny, ale wydajność kręgu może być kolejnym punktem decyzyjnym. Powiedział, że firma zachowuje równowagę między objętością a wymianą cewek, aby właściwie zarządzać wydajnością i zapasami.
10. Dalszy proces
Kenny powiedział, że stemplowanie może zapewnić lepszą kontrolę procesu, co jest ważne dla kolejnych operacji, takich jak spawanie i montaż.
Wniosek: oba są lepsze
Wszyscy trzej producenci matryc powiedzieli, że posiadanie podwójnych zdolności produkcyjnych może poprawić ich produkty i ich zdolność do utrzymania klientów.
Axelberg powiedział: „Wspaniale jest mieć możliwości produkcyjne i stemplujące”. „Nie chcę być czystym stemplem. Lub odwrotnie. Kiedy wydajność fabryk jest naprawdę wysoka lub jeśli forma się zepsuje, możemy użyć maszyn do tłoczenia lub maszyn laserowych i giętarek do produkcji części”.
Wszyscy trzej powiedzieli, że wszyscy cytowali projekt.
„Do obliczania tego używamy kilku różnych metod” – powiedział Haarsma. „Produkcja jest łatwiejsza do wyceny, bo masz oprogramowanie, które może wykonać za Ciebie dużo pracy. Do tłoczenia muszę ułożyć pasek, aby oszacować wydajność materiału, więc zajmuje to więcej czasu niż produkcja”.
Kenny powiedział, że Kapco dostarczyło technologię tłoczenia i produkcji, aby wspierać swoich klientów w zakresie tej samej części w różnych momentach cyklu życia produktu. „Nierzadko używamy technologii fab do wyprodukowania pierwszej części w celu sprawdzenia części i dostarczenia prototypów małych partii do czasu, gdy potrzebna jest większa ilość programu. Następnie inwestujemy w matryce. Lub, gdy objętość jest zmniejszona Podczas tłoczenia stanie się niewykonalne pod koniec cyklu życia produktu, wrócimy do produkcji części. Nasi klienci mogą korzystać ze zoptymalizowanych procesów produkcyjnych w małych lub dużych ilościach."
Axelberg przewidział, że kolejna nowa technologia może zmienić „fabrykę”? „Nie mamy jeszcze drukarki 3D do metalu, ale widzę, że ta technologia znacznie obniża koszty formowania narzędzi do małych partii o złożonej geometrii.
Link do tego artykułu: W jaki sposób producent obróbki metali decyduje się na zastosowanie technologii wytwarzania lub tłoczenia?
Oświadczenie o przedruku: Jeśli nie ma specjalnych instrukcji, wszystkie artykuły na tej stronie są oryginalne. Proszę wskazać źródło przedruku: https://www.cncmachiningptj.com/,thanks!
Precyzja 3, 4 i 5-osiowa Obróbka CNC usługi dla obróbka aluminium, beryl, stal węglowa, magnez, obróbka tytanu, Inconel, platyna, superstop, acetal, poliwęglan, włókno szklane, grafit i drewno. Zdolne do obróbki części do 98 cali. średnica toczenia. i +/- 0.001 cala tolerancja prostoliniowości. Procesy obejmują frezowanie, toczenie, wiercenie, wytaczanie, gwintowanie, gwintowanie, formowanie, radełkowanie, pogłębianie, pogłębianie, rozwiercanie i cięcie laserowe. Usługi drugorzędne, takie jak montaż, szlifowanie bezkłowe, obróbka cieplna, galwanizacja i spawanie. Prototyp i produkcja od małych do dużych ilości oferowana z maksymalnie 50,000 XNUMX sztuk. Nadaje się do zasilania płynów, pneumatyki, hydrauliki i zawór Aplikacje. Obsługuje przemysł lotniczy, lotniczy, wojskowy, medyczny i obronny. PTJ opracuje strategię, aby zapewnić najbardziej opłacalne usługi, które pomogą Ci osiągnąć swój cel, Zapraszamy do kontaktu z nami ( sprzedaz@pintejin.com ) bezpośrednio do nowego projektu.
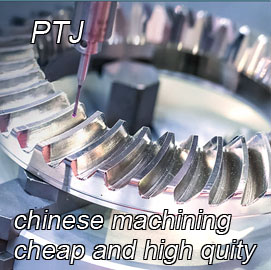
- Obróbka 5-osiowa
- Frezowanie CNC
- Toczenie CNC
- Obróbka przemysłowa
- Proces obróbki
- Obróbka powierzchniowa
- Obróbka metali
- Obróbka tworzyw sztucznych
- Formy do metalurgii proszków
- Die Casting
- Galeria części
- Auto części metalowe
- Części maszynerii
- Radiator LED
- Części budowlane
- Części mobilne
- Części medyczne
- Części elektroniczne
- Obróbka na miarę
- Części rowerowe
- Obróbka aluminium
- Obróbka tytanu
- Obróbka stali nierdzewnej
- Obróbka miedzi
- Obróbka mosiądzu
- Obróbka super stopów
- Obróbka podglądowa
- Obróbka UHMW
- Jednolita obróbka
- Obróbka PA6
- Obróbka PPS
- Obróbka teflonowa
- Obróbka Inconelu
- Obróbka stali narzędziowej
- Więcej materiału