Technologia cięcia stale ewoluuje, aby radzić sobie z twardszymi materiałami i coraz bardziej rygorystycznymi wymaganiami jakościowymi
Formowanie, rowkowanie, perforowanie, przebijanie, wiercenie, gwintowanie, ukosowanie, szlifowanie, spawanie, bez względu na to, co chcesz zrobić z rurą, aby była gotowa do dostawy do klienta, pierwszą operacją może być proces cięcia. Chociaż od dziesięcioleci dostępnych jest wiele metod cięcia, wiele z używanych dziś maszyn jest znacznie bardziej zaawansowanych niż te sprzed zaledwie kilku lat. Wraz z dywersyfikacją materiałów rurowych i wyzwaniem presji konkurencji funkcje oprogramowania, czujników i systemów sterowania stają się coraz potężniejsze. wynik? Dostawcy sprzętu mają większy wybór sprzętu i oprogramowania, co pozwala im opracowywać szybsze, dokładniejsze, bardziej wszechstronne i bardziej zautomatyzowane maszyny niż kiedykolwiek wcześniej, aby pomóc producentom rur stalowych w spełnianiu coraz bardziej wymagających zastosowań związanych z cięciem.
Ciągły rozwój technologii wprowadza na rynek ulepszone lub zupełnie nowe produkty, a w wielu przypadkach są to produkty wykonane z ulepszonych materiałów. W przemyśle metalowym główną siłą napędową rozwoju stopów jest przemysł motoryzacyjny, który wykorzystuje materiały, które są mocniejsze i lżejsze niż konwencjonalne metale, aby osiągnąć niższe cele emisji i wyższe cele wydajności paliwowej. Chociaż producenci samochodów używają różnych materiałów (takich jak aluminium i magnez), znaczna część każdego samochodu jest nadal wykonana ze stali. Innym czynnikiem napędzającym jest przemysł naftowy, który opiera się na chemikaliach stalowych. Dzięki wierceniu głębiej niż kiedykolwiek wcześniej, produkty petrochemiczne mogą wytrzymać trudne warunki środowiska morskiego.
Stalowy postęp.
W odpowiedzi na te wymagania przemysł stalowy nadal dostarcza na rynek nowe materiały. Według World Steel Association do wyboru jest 3,500 gatunków stali.
Zaawansowane wysokowytrzymałe stopy stali, wysokowytrzymałe/niskostopowe materiały, stale dwufazowe i stale plastyczne wywołane przemianami fazowymi mają niewielki wkład w materiałoznawstwo. Najnowsze materiały są znacznie mocniejsze niż zwykłe stale niskowęglowe, takie jak SAE 1010, która ma ostateczną wytrzymałość na rozciąganie około 42,000 XNUMX funtów na cal kwadratowy (PSI).
„Dziesięć lat temu średnia wytrzymałość motoryzacji na rozciąganie kucie przemysł wynosił 750 niutonów na milimetr kwadratowy (109,000 130 PSI), a maksymalna prędkość piły wielu pił wynosiła około 140 do 445 metrów na minutę (MPM) [XNUMX stóp na minutę (FPM)]”, powiedział Daniel Johns, dyrektor ds. rozwoju biznesu w Kinkelder, USA.
W tamtym czasie zapotrzebowanie na brzeszczoty były ogromne, ale w ciągu zaledwie kilku lat uległo ogromnym zmianom. Niektóre z najnowszych materiałów zwiększyły swoją wytrzymałość o 30% do 980 N/mm2 (142,000 200 PSI), a piły pracują szybciej, zwykle przekraczając 656 MPM (XNUMX FPM).
Johns powiedział: „Piętnaście lat temu sprzedawaliśmy więcej ostrzy ogólnego przeznaczenia”. „Dzisiaj na rynku rośnie zapotrzebowanie na ostrza przeznaczone do konkretnych zastosowań”. Powiedział na przykład, że zaledwie pięć lat temu ostrza z metalu ceramicznego (metalowe (ceramiczne) spełniają około 80% wymagań dla zastosowań w prętach, a obecnie około 80% zastosowań wymaga użycia powlekanego węglika.
Powiedział: „Wkładki z węglika powlekanego mają wyższą wytrzymałość końcówki i wyższą odporność na ciepło, dzięki czemu mogą wytrzymać cięcie twardszych materiałów przy wyższych prędkościach”.
Oprócz powłok, które mogą wytrzymać temperaturę do 900 stopni Celsjusza (1,600 stopni Fahrenheita), inna strategia obejmuje optymalizację geometrii zębów, zmianę kąta cięcia w celu dopasowania do gatunku stali oraz zmianę rozstawu, aby poradzić sobie z większymi prędkościami ostrza .
Nie oznacza to, że wyeliminowano cermetale. Powiedział: „Mają długą żywotność ostrza, więc gdy materiał nie jest tak twardy i ostrze nie działa zbyt szybko, nadal jest to dobry produkt”.
Johns powiedział, że cięcie niekoniecznie jest jednym procesem. W niektórych przypadkach nagrzewanie spowodowane tarciem spowoduje zwiększenie składowej deformacji podczas procesu skrawania. Zanim ząb wyciągnie wióry, materiał nagrzewa się, mięknie i odkształca. Niektóre zastosowania, takie jak cięcie stali duplex i gatunków niklu, wymagają dodatnich geometrii, gdzie cięcie jest głównie działaniem ścinającym. Zrozumienie tej różnicy i wielu innych czynników jest kluczem do wyboru ostrza. Personel Kinkelder stwierdził, że wymiana ostrza poważnie wpłynie na żywotność ostrza.
Johns powiedział: „Jeden z naszych klientów tnie stal nierdzewną 17-4, a każde ostrze może przeciąć około 7,400 ostrzy”. „Zaproponowaliśmy zmianę innych kształtów geometrycznych, aby rozwiązać bardzo rygorystyczne tolerancje zadziorów. Teraz klient może uzyskać około pięciokrotną żywotność, a każde ostrze może ciąć około 37,000 XNUMX razy”.
To ekstremalna sytuacja.
Jeśli ostrze nie jest najlepszym ostrzem do danego zastosowania, prawdopodobnie wzrośnie o 20%. Niezależnie od rzeczywistej ilości ulepszeń, firma Johnsa postrzega siebie jako konsultanta w zakresie cięcia, a następnie producenta ostrzy. Brzmi to sprzecznie z intuicją: przychody firmy opierają się na sprzedaży większej liczby ostrzy, a nie mniejszej liczby ostrzy. Jednak to jeszcze nie koniec. Podobnie jak wszyscy inni dostawcy produktów, firma ma swoje miejsce w sukcesie swoich klientów, więc wykorzysta swoją wiedzę z zakresu piłowania na korzyść klientów.
Firma przeprowadziła również pewne badania z producentem tartaku Rattunde Corp. Obie firmy współpracowały w celu ulepszenia funkcji systemu cięcia, takich jak cięcie prostokątne. Jedną z zalet Kinkelder jest to, że używa piły Rattunde, która może śledzić obrót brzeszczotu. System Rattunde śledzi położenie każdego zęba tak dokładnie, że może zapewnić, że początkowy kontakt z obrabianym przedmiotem jest równomiernie rozłożony na wszystkie zęby podczas wykonywania dużej liczby cięć w celu przetestowania trwałości brzeszczotu.
Polepszanie jakości.
Jon Hisey, dyrektor ds. rozwoju biznesu w Rattunde Corp., powiedział: „Jakość cięcia zawsze była popytem, ale w ostatnich latach naprawdę zaczęła się rozprzestrzeniać. Ostatni dołek 20 czy 30 lat temu jest do zaakceptowania”. . „W dzisiejszych czasach coraz więcej użytkowników wymaga czystych, 90-stopniowych nacięć bez zadziorów”. Hisey podejrzewa, że ma to związek z automatyzacją niższego szczebla.
Powiedział: „Producenci używają więcej robotyki, a spawacze robotów nie są dobrzy w radzeniu sobie z niespójnościami”. „Jeśli luka jest zbyt duża lub zmiany są duże, robot będzie bezsilny. Zależy to tylko od sposobu, w jaki jest zaprogramowany w kółko. Zrób to samo”.
Hisey powiedział, że chociaż wielu producentów nadal uważa na automatyzację, dla wielu producentów automatyzacja stała się nieunikniona.
Wyjaśnił: „Wielu producentów nadal polega na pracy ręcznej, aby usunąć rury z maszyny do cięcia i ułożyć je w stos”. „Jeśli masz trzech facetów, którzy to robią i dzwonią, gdy zachorujesz, tracisz jedną trzecią porodu. Pod tym względem”. Automatyzacja kilku kroków, które zwykle wykonuje się po cięciu (np. pomiar, wytrawianie, pakowanie) może uwolnić producentów od tego dylematu nie tylko dzisiaj, ale każdego dnia.
Oszczędność miejsca jest zawsze problemem, a Rattunde odpowiedział na to, wprowadzając na rynek małą maszynę w 2019 roku.
„Do niedawna nasza najmniejsza maszyna miała długość 2 metrów” – powiedział Hisey, odnosząc się do najdłuższej długości, jaką może ciąć. „Mamy kilku klientów, którzy używają tej maszyny do wytwarzania 2-calowych części produktu. Nasz najnowszy produkt to maszyna o długości 1 m, która jest bardziej praktyczna w przypadku małych części niż maszyna 2 m, zapewniając szybsze czasy cyklu i zmniejszając powierzchnię podłogi”.
Ulepszenia w hydraulice.
Przez długi czas spawanie było podstawowym procesem łączenia w branży hydraulicznej, ale stopniowo zostało zastąpione przez zaciskanie. Zaciskanie nie wymaga klejów, lutu i ciepła. Koszt wykonania połączeń zaciskanych jest wyższy niż połączeń lutowanych (koszt zaciskania części jest wyższy niż koszt niewielkiej ilości lutu i niektórych topników), ale jest to szybszy proces, więc może zwiększyć koszty pracy. Głównym zastrzeżeniem jest to, że zaciskanie wymaga, aby koniec rury był bardzo prosty i wolny od zadziorów. Linia produkcyjna produkowana przez producenta sprzętu Reika GmbH służy do rozwijania i prostowania rur miedzianych oraz do cięcia prostego i bez zadziorów, niezależnie od tego, czy materiał jest cienkościenną, czy grubościenną miedzią.
Joseph Kemple, prezes Heiko Machine, przedstawiciela firmy Reika w USA, powiedział: „W przypadku cienkościennej miedzi system wykorzystuje proces bezwiórowy”. Do zastosowań grubościennych linia produkcyjna wykorzystuje opatentowaną przez firmę piłę pierścieniową. Brzeszczot piły pierścieniowej jest okrągły, ale w przeciwieństwie do większości pił tarczowych jest napędzany wzdłuż średnicy zewnętrznej, a zęby znajdują się na średnicy wewnętrznej. Zęby są gotowymi wkładkami z węglików spiekanych z czterema powierzchniami skrawającymi i są montowane na obrabianej maszynie zawór siedzisko ze śrubą dociskową. Kiedy powierzchnia staje się stępiona, operator usuwa ząb, obraca go o 90 stopni i ponownie instaluje.
Unikalną funkcją piły jest ruch brzeszczotu. Oprócz obracania się, ostrze porusza się również mimośrodowo. Gdy ostrze obraca się wokół przedmiotu obrabianego, powoduje to stopniowe zbliżanie się ostrza do przedmiotu obrabianego. Połączenie kształtu zębów tnących i ruchu ostrza ma na celu uzyskanie średnicy zewnętrznej bez zadziorów, a ID bez zadziorów znikomych.
Kemple powiedział: „Nie pozostawi długiej listy odpadów, kilku zadziorów i bardzo małych gruzu”. Dodał: „Te małe zanieczyszczenia wypadają z maszyny nieszkodliwie, nie zakłócają pracy i są bardzo łatwe w obsłudze”.
Jedno lub dwa cięcia
Nożyce, znane ze swojej szybkości i bezwiórowego cięcia, były używane do zastosowań o dużej objętości/niskim mieszaniu, ale dziś nadają się również do wielu zastosowań z małymi partiami/wysokim mieszaniem. Maszyna się nie zmieniła; różnica polega na dodaniu nowoczesnego systemu sterowania i niezbędnego oprogramowania.
W przypadku zakładów przetwórczych, które opierają się na jednej lub dwóch piłach, nożyczki mogą nie być opłacalną opcją. Jednak producent, który w ciągu dnia mocno popycha kilka pił, może zaoszczędzić znaczną powierzchnię i materiały, przestawiając się na nożyce.
Prezes Haven Manufacturing Corp. Steve Thiry powiedział: „Nożyce o dużej prędkości mogą osiągnąć wydajność od trzech do sześciu pił”. Kolejną zaletą jest to, że nożyce nie mają nacięć, dzięki czemu żadna mała część nie jest marnowana. Ilość ciętego materiału za każdym razem.
Podobnie jak w przypadku wszystkich innych decyzji, wybór najlepszej maszyny do cięcia wymaga rozważenia kilku czynników, z których jednym jest rozmiar części. W przypadku producentów rur, którzy muszą wykonać mniej niż 50,000 50,000 prostych cięć rocznie, piły mają zdecydowanie większe szanse na osiągnięcie celów produkcyjnych i zwrotów z inwestycji niż nożyce. Jeśli objętość przekroczy XNUMX XNUMX, nożyce będą stawały się coraz bardziej atrakcyjne.
Thiry powiedział: „Jeśli producent musi co roku ciąć 60,000 70,000 do XNUMX XNUMX w różnych długościach i średnicach, można użyć nożyc”.
Haven jest znane z projektowania i produkcji dwóch różnych rodzajów nożyc: nożyc podpartych, w których wykorzystuje się trzpień, aby zapobiec deformacji spowodowanej przecinaniem i dzieleniem rurki przez ostrza nożyc; podwójne nożyce, które wykorzystują kierunek poprzeczny Nóż wbija się w nożyce. Do cięcia używa się ścianki rury i nożyczek. Początkowe cięcie uszkodzi integralność ścianki rury, dzięki czemu ścinanie można przeprowadzić bez zapadania się w rurze.
Pokrój długie i krótkie części.
Maszyny firmy mają średnicę od 0.25 do 5 cali. Większość produkowanych przez nią maszyn ma średnice zewnętrzne od 0.5 do 2.5 cala. Najczęściej stosowane są długości od 12 do 18 cali – długość wykorzystywana do produkcji amortyzatorów, co jest głównym zastosowaniem – maszyny firmy są często używane do cięcia odcinków od 0.5 cala do 10 stóp. Mogą osiągnąć dokładność długości do ±0.002 cala.
Używana maszyna Haven tnie cienkościenne rury o długości zaledwie 3/8 cala w celu wykonania zacisków do węży. Maszyna tnie 7,000 razy na godzinę bez deformacji lub strat materiału. Piły mogą wytwarzać części, ale nie mogą być wykonane z taką prędkością, a rzaz powoduje marnowanie znacznej ilości materiału, który stanowi procent każdego cięcia. Laser może również wykonywać cięcie nieniszczące. Chociaż czas cyklu jest bardzo krótki, tysiące prostych cięć na godzinę nie może w pełni wykorzystać największej zalety maszyny laserowej: wszechstronności.
Zaangażowany w odchudzoną produkcję. Nożyce są również dobrym wyborem do zastosowań o małej objętości/wysokim mieszaniu, ponieważ sposób ich użytkowania zmieniał się od dziesięcioleci. Znany z oszałamiającej wydajności (w niektórych przypadkach do 40 milionów części rocznie), pomogło to kilkadziesiąt lat temu w masowej produkcji. Dzisiejsze nożyce wciąż są przyprawiające o zawrót głowy i brudzą, ale wyposażone w nowoczesne systemy sterowania, ta sama maszyna może pomóc w odchudzaniu i wspomaganiu odchudzania. Jednoczęściowa soczewka typu flow dla zwierząt.
„Kilka lat temu maszyny te były dedykowane i mogły szybko produkować pojedyncze części przez kilka godzin. To były czasy ręcznej konwersji” – powiedział Tiri. Dziś jeden z jej klientów używa systemu podwójnego nożyc do budowy bud dla psów. Rurowy element budy składa się z pięciu odcinków, które są cięte na trzy odcinki. Nowoczesny sprzęt i oprogramowanie umożliwiają producentom cięcie różnych długości w kolejności, w jakiej są potrzebne. W wyniku operacji cięcia rur powstanie pięcioczęściowy zestaw, który można wykorzystać w następnej operacji. Szybki, dokładny i smukły.
Haven wykorzystuje również swoje doświadczenie w projektowaniu, aby opracować niestandardowe systemy obsługi materiałów po stronie podającej i może tworzyć całe zintegrowane jednostki tnące.
Aktualizacja cięcia laserowego dla produkcji i konstrukcji
Istnieje wiele rodzajów laserów do obróbki rur i elementów konstrukcyjnych. Jedną z najczęstszych maszyn jest zaciskanie długich rur za pomocą uchwytów i obsługa najpopularniejszych rozmiarów rur i rur, o maksymalnej średnicy zewnętrznej 4 cali. Duże maszyny obejmują LT24 BLM GROUP, które mogą ciąć średnice do 24 cali. W przypadku serii M4 firmy Bystronic, w tym FL400 i FL600, ich maksymalną średnicę można również zmniejszyć do 24 cali. Fabri Gear 400 II firmy Mazak może obsługiwać średnice do 16 cali. A TRUMPF TruLaser Tube 7000, jego maksymalna średnica cięcia wynosi 10 cali.
Wyprodukowano również inne maszyny do cięcia krótkich rur, takie jak zakrzywione elementy rurowe, hydroformowane elementy rurowe i inne kształty 3D. Dwie takie maszyny to VCL-T100 firmy Mazak, LT-Free firmy BLM GROUP i seria urządzeń TruLaser Cell firmy TRUMPF.
Cięcie rury. W pierwszych dniach cięcie laserowe materiały arkuszowe, produkty arkuszowe zwykle nie były wystarczająco płaskie, aby zoptymalizować proces. Gdy palnik porusza się po powierzchni papieru o standardowym rozmiarze z jednego końca na drugi, odległość palnika od powierzchni roboczej zmienia się zbyt mocno. Przemysł stalowy dostosował się do standardów handlowych dotyczących płaskości blach stalowych, a wkrótce potem podniósł standardy handlowe, aby dostosować się cięcie laserowe.
Tuba to inny produkt, wytwarzany na różne sposoby i wykorzystywany w różnych gałęziach przemysłu. Różne są również tolerancje.
John Quigley, wiceprezes ds. marketingu LVD Strippit, powiedział: „Przemysłowe specyfikacje rur nie są tak surowe jak rozmiary arkuszy”. „Producenci rur potrzebują systemów laserowych, które poradzą sobie z wszelkiego rodzaju zmianami”.
Procedura cięcia opiera się na idealnym rozmiarze, ale rury i produkty rurowe rzadko są proste, a produkty nieokrągłe zwykle wykazują pewien stopień zniekształcenia. W celu dokładnego cięcia i uniknięcia kolizji pomiędzy głowicą lasera a przedmiotem obrabianym, maszyna musi określić rzeczywisty kształt rury lampy i jej położenie względem głowicy tnącej, a następnie porównać go z oczekiwanym kształtem, aby skompensować zmiany wymiarowe. Maszyna LVD Strippit wykorzystuje pokładowy laserowy system pomiarowy do pomiaru kształtu łuku, a następnie porównuje pozycję uchwytu ze stabilną pozycją stacjonarną w celu określenia skrętu. Aby zoptymalizować kierunek rury względem spawu, laserowa maszyna firmy wykorzystuje system optyczny oparty na dwóch wejściach kamer.
Maszyna LVD Strippit ma przełomową wszechstronność systemu załadunku. Jest to pierwsza maszyna wyposażona w dwa ładowacze na jednej maszynie, jeden do opasywania, a drugi z siedmiopozycyjnym magazynem narzędzi. Do ładowania pojedynczej tuby. Wyposażona w automatyczną pakowarkę z jednej strony maszyny i kartoniarki z bindownicą z drugiej strony, dzięki czemu operator może czerpać to, co najlepsze z obu światów. Używając ładowarki belkowej do pracy produkcyjnej, może przerwać pracę i załadować kilka rur jedna po drugiej, aby zakończyć pracę awaryjną, a następnie kontynuować pierwszą pracę.
Podobnie firma Bystronic opracowała strategię załadunku i rozładunku, aby przyspieszyć przetwarzanie. Jego maszyna wykorzystuje cztery uchwyty, ale rura do obróbki nie musi cały czas używać czterech uchwytów.
Brendon DiVincenzo, kierownik ds. produktów laserowych i automatyzacji w Bystronic Inc., powiedział: „Chociaż głowica laserowa wykorzystuje dwa pierwsze uchwyty do obróbki końcowych elementów jednej rury, druga rura wykorzystuje dwa ostatnie uchwyty do załadowania do maszyny”. Ruchomy trzpień umożliwia dostosowanie maszyny do gięcia i skręcania pojedynczego przedmiotu obrabianego, przy jednoczesnym niewielkim naprężeniu uchwytu i poprawie dokładności obszaru cięcia.
TruLaser Tube 7000 firmy TRUMPF oferuje również dodatkowe funkcje rozszerzające możliwości obróbki rur. Inne narzędzia mogą umożliwiać gwintowanie otworów w grubościennych rurach oraz wiercenie i gwintowanie cierne rur cienkościennych. Posiada również opcjonalny trzpień, który można wsunąć w obrabiany przedmiot, aby chronić ID przed rozpryskami podczas procesu cięcia.
Duża średnica, gruba ścianka. Firma Mazak Optonics Inc. szacuje, że w ciągu pięciu lat od 2018 do 2023 r. wykorzystanie stali konstrukcyjnej będzie rosło w łącznym rocznym tempie wzrostu wynoszącym 5.3%. Siłą napędową, którą przytoczył, był rząd federalny i przemysł budowlany. Pierwsza dotyczy infrastruktury, a druga budynków mieszkalnych i niemieszkalnych. W takich zastosowaniach dwa czynniki ułatwiające cięcie laserowe rur stalowych to możliwość recyklingu i szybkość budowy. Około 90% metalu podlega recyklingowi, a precyzyjne cięcie laserowe ułatwia szybkie łączenie.
Precyzja maszyny laserowej w produkcji pogłębiaczy dla łączniks, ukośne nacięcia do łączenia i ukosowane końce do przygotowania do spawania sprawiają, że montaż na miejscu i spawanie są szybsze niż w przypadku tradycyjnych procesów.
Do tego typu zastosowań maszyna Mazak zapewnia sześć osi sterowania i cztery uchwyty samocentrujące, które radzą sobie z niespójnością rur i profili, takich jak puste przekroje konstrukcyjne, dwuteowniki, dwuteowniki i kątowniki. Według Mazak, w porównaniu z laserami światłowodowymi, technologia bezpośredniego lasera diodowego firmy jest o 45% bardziej energooszczędna niż lasery CO2, a jej gęstość mocy jest o 40% wyższa niż w przypadku laserów światłowodowych.
Aby dostosować się do różnych geometrii obrabianych przedmiotów, maszyny TRUMPF wykorzystują samocentrujące uchwyty zaciskowe, aby zapobiec uszkodzeniu rury. System mocowania w połączeniu z czujnikiem może zapewnić ciągłe monitorowanie w celu wprowadzenia niezbędnych zmian na ścieżce głowicy laserowej, aby zapobiec kolizjom.
Amerykańska grupa BLM wprowadziła niedawno na rynek model LT8.20, który ma funkcje 3D i może obsługiwać prawie każdy kształt. Przeznaczony jest do obsługi skomplikowanych wzorów cięcia, trudno dostępnych miejsc oraz spawania cięć przygotowawczych na rurach grubościennych. Wykorzystuje trzy funkcje z serii Active firmy: Active Tilt, który służy do szybkiego przetwarzania małych funkcji; spawanie aktywne, które ma na celu optymalizację separacji odpadów w dużych spawach; oraz Active Focus, który radzi sobie ze zmianami materiału i grubości.
Poprzez zainstalowanie ładowarki łańcuchowej z przodu w celu skonfigurowania systemu, powierzchnia zajmowana przez system może zostać zmniejszona o 20% i umożliwia załadunek i rozładunek z tej samej strony. Dzięki temu system jest bardziej efektywny w przypadku produkcji małoseryjnej i produkcji małoseryjnej.
Cięcie CO2 czy cięcie stałe? W dziedzinie laserów lasery CO2 ustąpiły miejsca technologii ciała stałego. W większości przypadków oznacza to lasery światłowodowe, ale TRUMPF ma swój własny TruDisk, podczas gdy Mazak ma bezpośrednie lasery diodowe. Lasery na ciele stałym znane są z uproszczonego dostarczania wiązki i znacznie niższych wymagań konserwacyjnych niż odmiany CO2. Zapewnia dłuższy czas pracy bez przestojów i niższe koszty konserwacji. Nie oznacza to jednak, że wkrótce pojawią się lasery CO2.
DiVincenzo powiedział: „Zapotrzebowanie rynku na lasery światłowodowe rośnie, ale lasery CO 2 nadal mają miejsce w produkcji, a nie dominującą pozycję w przeszłości”. To nie tylko kwestia wymiany rezonatora. Częstotliwość lasera światłowodowego sprawia, że konstrukcja maszyny bardzo różni się od konstrukcji rezonatora CO2. Lasery światłowodowe wymagają całkowicie zamkniętego obszaru cięcia, co sprawia, że załadunek i rozładunek materiałów jest bardziej skomplikowany. Uznane zalety technologii światłowodowej nie mają zastosowania tylko przy cięciu bardzo dużych elementów.
Powiedział: „Logistyka obsługi materiałów jest lepsza dla laserów CO2”.
zbieranie danych
Przemysł produkcyjny kwitnie w zakresie danych, niezależnie od tego, czy chodzi o pomiar czasu pracy maszyny, mierzenie czasu cyklu określonej części, dokonywanie pomiarów w celu znalezienia komponentów niespełniających norm, czy też tysiące innych punktów danych wykorzystywanych przez producentów do mierzenia i ulepszania operacji. informacje w.
W ciągu ostatnich kilku lat pojemność i objętość gromadzenia danych wzrosły o kilka rzędów wielkości. Połączenie wielu technologii: czujniki na maszynach generujące dane cyfrowe, znaczniki RFID na częściach lub pudełkach z częściami, które generują dane śledzące, łatwe do skanowania kody QR zawierające różne informacje, systemy Wi-Fi, które przenoszą dane z miejsca na miejsce, oraz Oprogramowanie, które porządkuje wszystkie funkcje – pozwala producentom na instalowanie systemów, o jakich jeszcze kilka lat temu nie było można usłyszeć.
Gromadzenie danych z kluczowych punktów procesu produkcyjnego, ich digitalizacja i przekształcanie w użyteczny strumień informacji, który jest stale aktualizowany i łatwo dostępny, może nie tylko wyeliminować papier lub zapewnić migawki działań produkcyjnych w czasie rzeczywistym. Dane można zintegrować z systemem planowania zasobów przedsiębiorstwa (ERP) firmy w celu modyfikacji planów produkcji, raportowania wyczerpanych stanów magazynowych surowców w celu wyzwalania działań zakupowych oraz informowania klientów o statusie zamówień, aby mogli powiadamiać swoich klientów i aktualizować swoje plany . Informacje te mają duże znaczenie na wcześniejszych i dalszych etapach łańcucha wartości: producenci mogą dobrowolnie rozpocząć wdrażanie technologii Przemysłu 4.0 dla własnych korzyści lub producenci mogą podążać tą ścieżką, aby zaspokoić potrzeby klientów.
Ten trend odgrywa ważną rolę w branży budowlanej. Dziś architekci robią coś więcej niż tylko szkice. Korzystają z oprogramowania do modelowania informacji o budynku (BIM), które jest bardzo złożoną wersją CAD, która zawiera pewne elementy ERP. Dostarcza tak wiele detali z tak dużą precyzją, że kontrahenci mogą prezentować na placu budowy dostawy takie jak przewody, rury i przewody, które są przycinane na odpowiednie długości, a nawet składane w elementy, dzięki czemu każdy element można zamontować w dowolnym momencie. Wykonują więcej pracy w swoich sklepach, ale znacznie mniej pracy na placu budowy, a wraz z postępem budowy każdy wykonawca będzie dostarczał aktualizacje.
Carroll Stokes, kierownik sprzedaży w T-Drill Industries Inc., powiedział: „Każdy instalator może zaktualizować model, aby wyzwolić następne zamówienie materiałowe, które wyzwala następne zlecenie produkcyjne i tak dalej”.
Wymogi wykonawcy mechanicznego kilka lat temu doprecyzowały możliwości T-Drill. Wykonawca potrzebował w pełni zautomatyzowanej maszyny, która mogłaby ciąć dziesiątki unikalnych elementów rur (proste części i połączenia rozgałęzione), drukować i wklejać etykiety (lub dwie etykiety, w przypadku dłuższych części, dwie na każdym końcu), etykietę A) i używać bocznika tabeli, aby je sklasyfikować.
Początkowo pracownicy T-Drill byli tajemnicą. Dlaczego warsztat hydrauliczny potrzebuje maszyny, która brzmi jak odpowiednia dla producenta? Później, gdy pracownicy zrozumieją pełny zakres BIM, zrozumieją, w jaki sposób zautomatyzowane maszyny wspierają ten rodzaj pracy. Dostęp do modelu pomaga każdemu, od właściciela budynku po najmniejszego wykonawcę, zrozumieć stan każdego etapu projektu, bez względu na to, jak duży jest projekt.
Sprzęt jest również stale aktualizowany. Stokes powiedział, że wkładanie rury do maszyny, ustawianie jej do cięcia, wykonywanie cięcia, przesuwanie i cofanie narzędzia kołnierzowego – te czynności są dokładne, w pełni kontrolowane i niedrogie, gdy siłownik jest serwomotorem.
Powiedział: „Mamy 27 serwerów na jednej maszynie”. „Na początku lat 1990. koszt każdej osi serwera wynosił około 5,000 USD. Obecnie cena każdej osi wynosi od 1,500 do 2,000 USD”. Dane wyjściowe zawierają dwa główne atrybuty serwomechanizmu, a mianowicie szybkość i dokładność. Powiedział: „Możemy dokładnie wyprodukować 3,000 produktów w ciągu godziny”.
Powiedział, że siłownik pneumatyczny jest równie szybki i dokładny, ale system serwo może kontrolować cały proces ruchu, aby zoptymalizować posuw i skok cięcia. Nie oznacza to, że funkcje cięcia i pętli maszyny są bardziej krytyczne niż łączność. Oba idą w parze.
Stokes powiedział: „O ile mi wiadomo, licytowanie dowolnego budynku komunalnego wymaga BIM. To był wymóg przez ostatnie sześć do ośmiu lat”. Punkt połączenia nie jest trudny. Dla firm działających w branży budowlanej interfejs z BIM staje się coraz ważniejszy. Dlatego dla ich dostawców coraz większego znaczenia nabierają inwestycje w sprzęt z łącznością cyfrową.
„To nie tylko dla budownictwa” – dodał Stokes. „Wykorzystywany jest również w przemyśle stoczniowym i ma podobne względy – konstrukcja i hydraulika, pneumatyka, instalacje elektryczne, wodne, przeciwpożarowe i kanalizacyjne”.
Aby zademonstrować te technologie, firma TRUMPF założyła w pełni sieciową fabrykę produkcyjną w Hoffman Estates w stanie Illinois. Chociaż nie jest to operacja zorientowana na lampę, przynajmniej jeszcze nie. Ilustruje możliwości digitalizacji wszystkich funkcji, które są krytyczne dla procesu produkcyjnego.
Po wezwaniu zgodnie z instrukcjami roboczymi, automatycznie prowadzony pojazd pobierze niezbędne płyty i podzieli je na segmenty, rozpoczynając w ten sposób proces, w którym materiał jest cięty, tłoczony i wyginany z jednej maszyny do drugiej. W większości przypadków konserwacja maszyn i obsługa materiałów są zautomatyzowane. Przejrzystość jest ważną częścią technologii wykorzystywanej w inteligentnych fabrykach.
Link do tego artykułu: Technologia cięcia stale ewoluuje, aby radzić sobie z twardszymi materiałami i coraz bardziej rygorystycznymi wymaganiami jakościowymi
Oświadczenie o przedruku: Jeśli nie ma specjalnych instrukcji, wszystkie artykuły na tej stronie są oryginalne. Proszę wskazać źródło przedruku: https://www.cncmachiningptj.com/,thanks!
Precyzja 3, 4 i 5-osiowa Obróbka CNC usługi dla obróbka aluminium, beryl, stal węglowa, magnez, obróbka tytanu, Inconel, platyna, superstop, acetal, poliwęglan, włókno szklane, grafit i drewno. Zdolne do obróbki części do 98 cali. średnica toczenia. i +/- 0.001 cala tolerancja prostoliniowości. Procesy obejmują frezowanie, toczenie, wiercenie, wytaczanie, gwintowanie, gwintowanie, formowanie, radełkowanie, pogłębianie, pogłębianie, rozwiercanie i cięcie laserowe. Usługi drugorzędne, takie jak montaż, szlifowanie bezkłowe, obróbka cieplna, galwanizacja i spawanie. Prototyp i produkcja od małych do dużych ilości oferowana z maksymalnie 50,000 XNUMX sztuk. Nadaje się do zasilania płynów, pneumatyki, hydrauliki i zawór Aplikacje. Obsługuje przemysł lotniczy, lotniczy, wojskowy, medyczny i obronny. PTJ opracuje strategię, aby zapewnić najbardziej opłacalne usługi, które pomogą Ci osiągnąć swój cel, Zapraszamy do kontaktu z nami ( sprzedaz@pintejin.com ) bezpośrednio do nowego projektu.
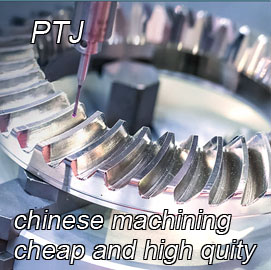
- Obróbka 5-osiowa
- Frezowanie CNC
- Toczenie CNC
- Obróbka przemysłowa
- Proces obróbki
- Obróbka powierzchniowa
- Obróbka metali
- Obróbka tworzyw sztucznych
- Formy do metalurgii proszków
- Die Casting
- Galeria części
- Auto części metalowe
- Części maszynerii
- Radiator LED
- Części budowlane
- Części mobilne
- Części medyczne
- Części elektroniczne
- Obróbka na miarę
- Części rowerowe
- Obróbka aluminium
- Obróbka tytanu
- Obróbka stali nierdzewnej
- Obróbka miedzi
- Obróbka mosiądzu
- Obróbka super stopów
- Obróbka podglądowa
- Obróbka UHMW
- Jednolita obróbka
- Obróbka PA6
- Obróbka PPS
- Obróbka teflonowa
- Obróbka Inconelu
- Obróbka stali narzędziowej
- Więcej materiału