Obszerny przewodnik na temat konfigurowania narzędzia tnącego tokarki
Ustawianie narzędzia skrawającego tokarskiego jest podstawową umiejętnością każdego mechanika, szczególnie w przypadku tokarek sterowanych numerycznie (CNC). Właściwe ustawienie narzędzia ma kluczowe znaczenie dla uzyskania precyzyjnych i dokładnych wyników obróbki. W tym obszernym przewodniku zagłębimy się w zawiłe szczegóły dotyczące ustawiania narzędzia tokarskiego do toczenia CNC. Od podstaw komponentów narzędzi tokarskich po zaawansowane techniki optymalizacji wydajności skrawania – ten artykuł ma na celu zapewnienie kompleksowego zrozumienia procesu. Pod koniec tego przewodnika będziesz posiadać wiedzę i umiejętności niezbędne do niezawodnego i precyzyjnego ustawienia narzędzia tokarskiego do cięcia, zapewniając optymalne wyniki w operacjach toczenia CNC.
Zrozumienie narzędzi skrawających tokarki
W świecie obróbki skrawaniem narzędzia tokarskie są niezbędnymi komponentami do kształtowania i przekształcania surowców w precyzyjnie zaprojektowane części. Niezależnie od tego, czy pracujesz z tradycyjnymi tokarkami ręcznymi, czy zaawansowanymi tokarkami CNC, niezbędna jest dogłębna znajomość narzędzi skrawających tokarki. W tej sekcji zagłębimy się w charakterystykę, funkcje i rodzaje narzędzi tokarskich.
Charakterystyka narzędzi skrawających do tokarek
Narzędzia skrawające tokarki są przeznaczone do wykonywania różnorodnych operacji obróbczych, takich jak toczenie, planowanie, rowkowanie, gwintowanie i inne. Narzędzia te mają kilka wspólnych cech:
- Twardość Narzędzia skrawające tokarki są zwykle wykonane ze stali szybkotnącej (HSS), węglika lub innych specjalistycznych materiałów narzędziowych. Materiały te dobiera się ze względu na ich twardość, która pozwala narzędziu wytrzymać wysokie temperatury i ciśnienia powstające podczas cięcia.
- Ostrze: Krawędź skrawająca narzędzia tokarskiego to część, która faktycznie usuwa materiał z przedmiotu obrabianego. Zostało zaprojektowane tak, aby było ostre i precyzyjne, a geometria krawędzi skrawającej może się różnić w zależności od konkretnego zadania, do jakiego narzędzie jest przeznaczone.
- Cholewka: Trzpień narzędzia tokarskiego to część mocowana w uchwycie narzędzia. Zapewnia stabilność i sztywność narzędzia podczas pracy proces obróbki. Konstrukcje chwytów mogą się różnić w zależności od rodzaju narzędzia i specyfikacji producenta.
- Uchwyt na narzędzia: Uchwyt narzędziowy jest kluczowym elementem, zwłaszcza w przypadku toczenia CNC, ponieważ bezpiecznie utrzymuje narzędzie tokarskie na miejscu. Musi zapewniać stabilność, precyzję i łatwość regulacji, aby zapewnić optymalną wydajność narzędzia.
- geometria: Geometria narzędzia skrawającego, w tym kąt natarcia, kąt przyłożenia i łamacz wiórów, odgrywają znaczącą rolę w określaniu wydajności narzędzia. Właściwa geometria jest niezbędna do uzyskania skutecznego usuwania materiału i odprowadzania wiórów.
- Powłoka: Wiele narzędzi tokarskich jest wyposażonych w specjalistyczne powłoki, takie jak TiN (azotek tytanu) lub TiAlN (azotek tytanu i glinu), które zwiększają trwałość narzędzia, zmniejszają tarcie i poprawiają wydajność.
Funkcje narzędzi skrawających tokarki
Narzędzia skrawające tokarki pełnią kilka podstawowych funkcji w procesie obróbki:
- Usuwanie materiału: Podstawową funkcją narzędzi skrawających tokarki jest usuwanie materiału z przedmiotu obrabianego. Usunięcie to może nastąpić poprzez toczenie (obracanie przedmiotu obrabianego podczas cięcia), planowanie (tworzenie płaskiej powierzchni) lub inne operacje.
- Kontrola wymiarowa: Narzędzia skrawające odpowiadają za to, aby wymiary obrabianej części odpowiadały pożądanym specyfikacjom. Precyzyjna kontrola jest niezbędna do osiągnięcia dokładnych i spójnych wyników.
- Wykończenie powierzchni: O jakości wykończenia powierzchni decyduje ostrość narzędzia skrawającego, jego geometria oraz zastosowane parametry skrawania. Dobrze konserwowane i właściwie ustawione narzędzie tnące przyczynia się do gładkiego i delikatnego wykończenia powierzchni.
- Kontrola wiórów: Skuteczna kontrola wiórów jest niezbędna, aby zapobiec gromadzeniu się wiórów i utrzymać czyste i bezpieczne środowisko pracy. Łamacz wiórów w niektórych narzędziach ułatwia usuwanie wiórów.
- Wydajność: Narzędzia skrawające tokarki zostały zaprojektowane tak, aby procesy obróbki były wydajne i opłacalne. Pomagają minimalizować straty materiału i optymalizować trwałość narzędzi, redukując koszty produkcji.
Rodzaje narzędzi skrawających do tokarek
Tokarskie narzędzia skrawające są dostępne w różnych typach, każdy dostosowany do konkretnych zadań obróbczych. Oto kilka popularnych typów:
- Narzędzia tokarskie: Narzędzia te są wszechstronne i wykorzystywane do operacji toczenia cylindrycznego. Potrafią kształtować zewnętrzną i wewnętrzną powierzchnię przedmiotu obrabianego.
- Narzędzia do wytaczania: Narzędzia wytaczające służą do powiększania lub wykańczania istniejących otworów. Zostały zaprojektowane z myślą o precyzji i dokładności obróbki otworów.
- Narzędzia do przecinania: Narzędzia do przecinania służą do oddzielania przedmiotu obrabianego od większego materiału. Tworzą określone linie podziału przy minimalnej ilości odpadów.
- Narzędzia do gwintowania: Narzędzia do gwintowania służą do wycinania gwintów na przedmiocie obrabianym. Występują w różnych kształtach i rozmiarach, dostosowanych do różnych wymagań dotyczących gwintowania.
- Narzędzia do rowkowania: Narzędzia do rowkowania tworzą rowki lub wgłębienia na przedmiocie obrabianym, zazwyczaj w celu umieszczenia pierścieni typu O-ring, pierścieni ustalających lub innych elementów.
- Narzędzia do twarzy: Narzędzia do planowania służą do tworzenia płaskich powierzchni na końcu przedmiotu obrabianego. Często stosuje się je w celu uzyskania prostopadłych powierzchni lub usunięcia materiału z końca przedmiotu obrabianego.
Zrozumienie cech i funkcji narzędzi skrawających tokarki jest niezbędne do wyboru odpowiedniego narzędzia do konkretnego zadania obróbczego. Wybór narzędzia skrawającego może znacząco wpłynąć na jakość i wydajność procesu obróbki, co czyni go krytyczną decyzją w każdej operacji tokarskiej. Ponadto właściwa konserwacja i konfiguracja narzędzi są niezbędne do zapewnienia spójnych i precyzyjnych wyników, co zostanie omówione bardziej szczegółowo w dalszej części tego przewodnika.
Rodzaje narzędzi skrawających do tokarek
Narzędzia skrawające do tokarek są dostępne w różnych typach, każdy specjalnie zaprojektowany do określonego zadania obróbki. Zrozumienie różnych typów narzędzi skrawających i ich zastosowań jest niezbędne do wyboru odpowiedniego narzędzia do danego zadania. Oto kilka popularnych typów narzędzi tokarskich:
Narzędzia tokarskie:
- Narzędzie okrągłe: Używane do ogólnych operacji toczenia. Posiada zaokrągloną krawędź tnącą i nadaje się zarówno do obróbki zgrubnej, jak i wykańczającej.
- Narzędzie diamentowe: Nazwany tak ze względu na krawędź tnącą w kształcie rombu, idealnie nadaje się do precyzyjnej obróbki różnych materiałów, w tym metali i tworzyw sztucznych.
- Narzędzie z końcówką kwadratową: Posiada kwadratową krawędź tnącą i jest zwykle używany do operacji toczenia czołowego i walcowo-czołowego.
Narzędzia do wytaczania:Wewnętrzny wytaczak: Służy do powiększania i wykańczania istniejących otworów w przedmiocie obrabianym. Został zaprojektowany z myślą o precyzji i może tworzyć dokładne wymiary wewnętrzne.
Narzędzia do przecinania:Ostrze przecinające: Narzędzia te służą do odcięcia przedmiotu obrabianego z większego zapasu. Tworzą określoną linię podziału przy minimalnej ilości odpadów.
Narzędzia do gwintowania:
- Narzędzie do wycinania gwintów: Przeznaczone do tworzenia gwintów zewnętrznych na przedmiocie obrabianym. Występują w różnych kształtach i rozmiarach, dostosowanych do różnych wymagań dotyczących gwintowania.
- Narzędzie do wyszukiwania wątków: Służy do ścigania lub przywracania istniejących wątków. Narzędzia te są powszechnie używane do naprawy gwintów.
Narzędzia do rowkowania:Narzędzie do rowkowania: Narzędzia te tworzą rowki lub wgłębienia na przedmiocie obrabianym, często w celu umieszczenia pierścieni typu O-ring, pierścieni ustalających lub innych elementów.
Narzędzia do twarzy:Narzędzie do twarzy: Służy do tworzenia płaskich powierzchni na końcu przedmiotu obrabianego. Jest często używany do uzyskania prostopadłych powierzchni lub usunięcia materiału z końca przedmiotu obrabianego.
Narzędzia do przecinania i rowkowania:Narzędzie kombinowane: Te wszechstronne narzędzia są przeznaczone zarówno do operacji przecinania, jak i rowkowania, oszczędzając czas i wymianę narzędzi.
Narzędzia do gwintowania i rowkowania:Kombinowane narzędzie do gwintowania i rowkowania: Idealne do prac wymagających zarówno gwintowania, jak i rowkowania tego samego przedmiotu obrabianego.
Narzędzia do fazowania:Narzędzie do fazowania: Służy do tworzenia fazowań lub fazowanych krawędzi na przedmiocie obrabianym. Fazy są często stosowane w celu poprawy wyglądu i łatwości montażu obrabianych części.
Narzędzia do radełkowania:Narzędzie do radełkowania: Radełkowanie to proces tworzenia teksturowanego wzoru na przedmiocie obrabianym, zwykle w celu poprawy przyczepności lub estetyki. Narzędzia do radełkowania są dostępne w różnych wzorach i konstrukcjach.
Narzędzia do formowania:Narzędzie formularza: Narzędzia te są projektowane na zamówienie dla określonych geometrii części, często używanych do wytwarzania skomplikowanych i niestandardowych kształtów.
Narzędzia specjalistyczne:Narzędzia profilowe: Służy do tworzenia złożonych profili na przedmiocie obrabianym.
Narzędzia do planowania i toczenia: Są one przeznaczone zarówno do operacji planowania, jak i toczenia.
Narzędzia do odcięcia: Przeznaczone do przecinania przedmiotu obrabianego w celu utworzenia oddzielnych części lub usunięcia nadmiaru materiału.
Wybór odpowiedniego narzędzia skrawającego zależy od takich czynników, jak obrabiany materiał, pożądane wykończenie, wymagane wymiary i konkretna wykonywana operacja. Aby zapewnić wydajną i dokładną obróbkę, istotny jest wybór odpowiedniego narzędzia i jego prawidłowa konserwacja. Właściwy dobór narzędzi wraz z prawidłową konfiguracją i regulacją ma kluczowe znaczenie dla uzyskania wysokiej jakości wyników w operacjach tokarskich.
Elementy narzędzia tnącego tokarki
Narzędzie skrawające tokarki to precyzyjne narzędzie przeznaczone do kształtowania, cięcia i usuwania materiału z przedmiotu obrabianego. Aby zrozumieć, jak to działa i jak prawidłowo go skonfigurować, ważne jest, aby zapoznać się z jego różnymi komponentami. Oto kluczowe elementy narzędzia tokarskiego:
- Uchwyt na narzędzia:Uchwyt narzędzia to część mocująca narzędzie tnące na miejscu. Mocuje się go do imaka narzędziowego tokarki i zapewnia niezbędną sztywność i stabilność podczas operacji obróbki. Uchwyty narzędziowe są dostępne w różnych wersjach, dostosowanych do różnych typów narzędzi skrawających.
- Cholewka:Chwyt jest częścią narzędzia tnącego, która pasuje do uchwytu narzędzia. Jest zazwyczaj cylindryczny i jest bezpiecznie zaciśnięty w uchwycie. Wymiary i kształt trzpienia mogą się różnić w zależności od typu i konstrukcji narzędzia.
- Ostrze:Krawędź tnąca to ostra część narzędzia, która styka się z materiałem obrabianym i usuwa go. Jakość krawędzi skrawającej i jej geometria znacząco wpływają na wydajność cięcia i wykończenie powierzchni. Utrzymanie ostrości i precyzji krawędzi tnącej jest niezbędne.
- Wstawić:Wiele nowoczesnych narzędzi skrawających wykorzystuje wymienne płytki, które są zwykle wykonane z twardych materiałów, takich jak węglik lub ceramika. Płytki te posiadają geometrię skrawającą i są mocowane w kieszeni narzędzia skrawającego. Można je obracać lub wymieniać, gdy ulegną zużyciu lub uszkodzeniu, co przedłuża żywotność narzędzia.
- Końcówka narzędzia:Końcówka narzędzia to wierzchołek narzędzia skrawającego, w którym spotykają się krawędź skrawająca i płytka (jeśli jest używana). Aby zapewnić precyzyjną obróbkę, końcówka narzędzia musi być dokładnie ustawiona i wyrównana. Niektóre narzędzia tokarskie mają regulowany promień ostrza narzędzia, co zapewnia lepszą kontrolę nad wydajnością narzędzia.
- Bok narzędzia:Bok narzędzia to powierzchnia boczna narzędzia skrawającego, która nie jest częścią krawędzi skrawającej. Odpowiednie kąty przyłożenia na boku narzędzia zapewniają odprowadzanie wiórów i zmniejszają tarcie pomiędzy narzędziem a obrabianym przedmiotem.
- Powierzchnia natarcia narzędzia:Powierzchnia natarcia to powierzchnia narzędzia tnącego zwrócona w stronę przedmiotu obrabianego. Kąt i stan powierzchni natarcia wpływają na powstawanie wiórów i wydajność procesu skrawania. Kąt natarcia jest krytycznym aspektem geometrii narzędzia.
- Kąt przyłożenia narzędzia:Kąt przyłożenia to kąt pomiędzy bokiem narzędzia a osią narzędzia. Zapewnia, że krawędź skrawająca nie ociera się o obrabiany przedmiot, redukując tarcie i wytwarzanie ciepła.
- Kąt przyłożenia narzędzia:Kąt przyłożenia to kąt pomiędzy powierzchnią natarcia a powierzchnią przedmiotu obrabianego. Umożliwia płynny przepływ wiórów i zapobiega kolizjom pomiędzy narzędziem a obrabianym przedmiotem.
- Łamacz wiórów (jeśli dotyczy):Niektóre narzędzia skrawające, szczególnie te używane do obróbki zgrubnej, posiadają łamacz wióra, rowek lub karb na powierzchni natarcia. Łamacz wiórów pomaga kontrolować tworzenie się wiórów i usprawniać ich odprowadzanie.
Właściwy montaż, wyosiowanie i konserwacja tych komponentów są niezbędne do osiągnięcia precyzyjnej i wydajnej obróbki. Wybór narzędzia tnącego i jego ustawienie muszą być dostosowane do konkretnej operacji obróbki i obrabianego materiału. Aby zapewnić spójne i wysokiej jakości wyniki, konieczne są również regularne kontrole i konserwacja elementów narzędzia tnącego.
Wybór odpowiedniego narzędzia tnącego do zadania
Wybór odpowiedniego narzędzia skrawającego to kluczowa decyzja w każdej operacji obróbki skrawaniem, ponieważ ma ona ogromny wpływ na jakość, wydajność i precyzję pracy. Wybierając odpowiednie narzędzie skrawające do konkretnego zadania, należy wziąć pod uwagę kilka czynników. Oto przewodnik, jak wybrać odpowiednie narzędzie skrawające do swojego projektu obróbki:
1. Materiał przedmiotu obrabianego:
Materiał poddawany obróbce jest jednym z najważniejszych czynników przy wyborze narzędzia. Różne materiały mają różną twardość, przewodność cieplną i ścieralność. Rozważ następujące:
- Twardość Twarde materiały, takie jak hartowana stal lub ceramika, wymagają narzędzi skrawających o twardych krawędziach skrawających, takich jak płytki z węglików spiekanych, aby wytrzymać duże siły skrawania.
- Miękkie materiały: W przypadku bardziej miękkich materiałów, takich jak aluminium lub tworzywa sztuczne, wystarczająca może być stal szybkotnąca (HSS) lub inne materiały narzędziowe.
2. Operacja obróbki:
Konkretna operacja, którą wykonujesz, taka jak toczenie, frezowanie, wiercenie, gwintowanie lub rowkowanie, będzie dyktować rodzaj potrzebnego narzędzia tnącego. Do różnych zadań przeznaczone są różne narzędzia, a wybór odpowiedniego zapewnia optymalną wydajność.
3. Prędkość skrawania i posuw:
Określ wymaganą prędkość skrawania i posuw w oparciu o materiał i operację obróbki. Producenci narzędzi skrawających podają zalecenia dotyczące tych parametrów w oparciu o konstrukcję narzędzia i obrabiany materiał. Przestrzeganie tych zaleceń jest kluczowe dla osiągnięcia pożądanych rezultatów.
4. Geometria narzędzia:
Weź pod uwagę geometrię narzędzia skrawającego, w tym kąt natarcia, kąt przyłożenia i promień ostrza narzędzia. Geometria narzędzia powinna być dostosowana do materiału i rodzaju cięcia. Na przykład dodatni kąt natarcia jest odpowiedni dla bardziej miękkich materiałów, podczas gdy ujemny kąt natarcia jest lepszy dla twardszych materiałów.
5. Wymiary przedmiotu obrabianego:
Rozmiar i wymiary przedmiotu obrabianego również wpływają na wybór narzędzia. Niektóre narzędzia skrawające lepiej nadają się do operacji zgrubnych w celu szybkiego usunięcia materiału sypkiego, inne natomiast są przeznaczone do wykańczania w celu uzyskania precyzyjnych wymiarów i wykończenia powierzchni.
6. Wymagania dotyczące wykończenia powierzchni:
Jeśli potrzebujesz określonego wykończenia powierzchni, wybierz narzędzie skrawające o odpowiedniej geometrii i ostrości. Narzędzia do wykańczania zostały zaprojektowane tak, aby zapewnić gładsze wykończenie powierzchni, podczas gdy narzędzia do obróbki zgrubnej są bardziej wydajne w usuwaniu materiału.
7. Materiał narzędzia:
Wybór materiału narzędzia jest kluczowy. Narzędzia z węglików spiekanych, stali szybkotnącej (HSS), ceramiki i narzędzi powlekanych mają swoje zalety i ograniczenia. Podejmując decyzję, należy wziąć pod uwagę takie czynniki, jak trwałość narzędzia, odporność na zużycie i koszt materiału narzędzia.
8. Płyn chłodzący i smarowanie:
Należy rozważyć, czy operacja cięcia wymaga chłodziwa czy smarowania. Niektóre materiały generują nadmierne ciepło podczas obróbki, a użycie odpowiedniego chłodziwa lub smaru może wydłużyć żywotność narzędzia i poprawić wydajność skrawania.
9. Powłoki narzędzi:
Wiele nowoczesnych narzędzi skrawających jest wyposażonych w specjalistyczne powłoki, takie jak TiN (azotek tytanu) lub TiAlN (azotek tytanu i glinu), które poprawiają odporność na zużycie i zmniejszają tarcie. Wybierz narzędzie z powłoką odpowiednią do konkretnego zastosowania.
10. Kwestie kosztów:
Kluczowe znaczenie ma zrównoważenie kosztu narzędzia tnącego z jego wydajnością i trwałością. Chociaż narzędzia premium mogą zapewniać dłuższą żywotność i lepszą wydajność, istotne jest znalezienie równowagi odpowiadającej budżetowi projektu.
11. Uchwyt narzędziowy i kompatybilność z maszyną:
Upewnij się, że wybrane narzędzie skrawające jest kompatybilne z systemem oprawek narzędziowych Twojej tokarki lub centrum obróbkowego. Uchwyt narzędzia powinien zapewniać stabilność i sztywność narzędzia skrawającego podczas procesu obróbki.
Ostatecznie wybór odpowiedniego narzędzia tnącego do danego zadania będzie zależał od kombinacji tych czynników. Zawsze zapoznaj się z zaleceniami producenta narzędzia i rozważ zasięgnięcie porady doświadczonych mechaników lub ekspertów w zakresie narzędzi, jeśli nie masz pewności. Właściwy dobór i konfiguracja narzędzi ma fundamentalne znaczenie dla osiągnięcia wydajnych i precyzyjnych wyników obróbki.
Ustawianie narzędzia tnącego tokarki
Ustawianie narzędzia skrawającego tokarki do toczenia CNC to systematyczny proces, który obejmuje kilka kluczowych etapów. Każdy krok jest niezbędny, aby zapewnić prawidłowe ustawienie i wyrównanie narzędzia tnącego, co ostatecznie prowadzi do precyzyjnej i wydajnej obróbki. Przeanalizujmy proces krok po kroku:
Krok 1: Przygotowanie tokarki i przedmiotu obrabianego
Przed ustawieniem narzędzia tnącego konieczne jest przygotowanie tokarki i przedmiotu obrabianego:
- Zabezpiecz obrabiany przedmiot: Upewnij się, że obrabiany przedmiot jest dobrze zamocowany w uchwycie tokarskim lub tulei zaciskowej. Upewnij się, że obraca się płynnie, bez drgań i wibracji.
- Bezpieczeństwo: Upewnij się, że zastosowano wszystkie środki bezpieczeństwa, w tym użycie odpowiedniego sprzętu ochrony osobistej (PPE) i prawidłowe ustawienia tokarki.
Krok 2: Wybór odpowiedniego uchwytu narzędziowego
Uchwyt narzędziowy jest krytycznym elementem w procesie konfiguracji. Wybierz odpowiednią oprawkę narzędziową w oparciu o takie czynniki, jak rodzaj narzędzia tnącego, wykonywana operacja i system imaka narzędziowego tokarki.
- Dopasuj uchwyt narzędziowy do narzędzia tnącego: Upewnij się, że uchwyt narzędzia jest zgodny z typem i rozmiarem narzędzia tnącego, którego zamierzasz używać.
- Sztywność uchwytu narzędziowego: Wybierz uchwyt narzędziowy zapewniający stabilność i sztywność. Jest to szczególnie ważne w zastosowaniach wymagających dużej precyzji.
Krok 3: Montaż narzędzia tnącego
Montaż narzędzia tnącego polega na zabezpieczeniu go w uchwycie narzędzia i zapewnieniu jego stabilnego i prawidłowego ustawienia:
- Zabezpiecz narzędzie tnące: Włóż narzędzie tnące do uchwytu narzędzia i dokręć wszelkie mechanizmy zaciskające, takie jak śruby ustalające lub tuleje zaciskowe. Upewnij się, że narzędzie jest bezpiecznie trzymane.
- Orientacja: Sprawdź, czy narzędzie tnące jest prawidłowo zorientowane w stosunku do przedmiotu obrabianego. Narzędzie powinno być ustawione tak, aby wchodziło w obrabiany przedmiot pod żądanym kątem i na żądanej głębokości.
Krok 4: Regulacja wysokości narzędzia i wyrównania linii środkowej
Prawidłowa wysokość narzędzia i wyrównanie linii środkowej mają kluczowe znaczenie dla uzyskania precyzyjnych wymiarów obróbki:
- Regulacja wysokości narzędzia: Wyreguluj wysokość narzędzia, aby dopasować je do linii środkowej wrzeciona tokarki. Aby ustawić narzędzie na właściwej wysokości, użyj wysokościomierza lub drążka testowego.
- Wyrównanie linii środkowej: Upewnij się, że narzędzie jest wyrównane z osią wrzeciona tokarki. Niewspółosiowość może skutkować obróbką niecentryczną, co wpływa na dokładność części.
Krok 5: Ustawianie kompensacji promienia ostrza narzędzia
W przypadku toczenia CNC kompensacja promienia ostrza narzędzia uwzględnia geometrię narzędzia skrawającego. Jest to szczególnie ważne w przypadku używania narzędzi wkładanych:
- Określ promień ostrza narzędzia: Zmierz lub sprawdź dokładny promień naroża używanej płytki narzędzia skrawającego.
- Wprowadź wartość promienia: W oprogramowaniu sterującym CNC wprowadź zmierzoną wartość promienia ostrza narzędzia, aby upewnić się, że maszyna kompensuje geometrię narzędzia podczas obróbki.
Krok 6: Ustawianie przesunięć narzędzi
Przesunięcia narzędzi uwzględniają różnice w wymiarach narzędzia i geometrii przedmiotu obrabianego. Zapewniają dokładne dopasowanie położenia narzędzia do obróbki:
- Wybierz prawidłowe przesunięcie narzędzia: Określ odpowiednią wartość korekcji narzędzia w oparciu o geometrię narzędzia i operację obróbki. Ta wartość przesunięcia kompensuje wszelkie rozbieżności.
- Wprowadź wartości odsunięcia: Wprowadź wybrane wartości przesunięcia do oprogramowania sterującego CNC. Wartości te poinstruują maszynę, jak dokładnie wyregulować położenie narzędzia.
Podczas całego procesu ustawiania narzędzia należy używać precyzyjnych przyrządów pomiarowych, takich jak mikrometry, wysokościomierze i czujniki zegarowe, aby weryfikować i dostrajać ustawienie narzędzia. Regularnie sprawdzaj i konserwuj narzędzie tnące, aby mieć pewność, że pozostaje ostre i w dobrym stanie, ponieważ dobrze konserwowane narzędzie przyczynia się do spójnych i dokładnych wyników obróbki.
Prawidłowe ustawienie narzędzia tnącego tokarki w tych krokach ma kluczowe znaczenie dla osiągnięcia optymalnych wyników w operacjach toczenia CNC. Precyzja i dbałość o szczegóły podczas ustawiania narzędzia to kluczowe czynniki w produkcji wysokiej jakości obrabianych części.
Optymalizacja parametrów skrawania dla toczenia CNC
Optymalizacja parametrów skrawania jest niezbędna do osiągnięcia wydajnych i wysokiej jakości operacji toczenia CNC. Cztery kluczowe aspekty, które należy wziąć pod uwagę podczas optymalizacji parametrów skrawania, to prędkości i posuwy, głębokość skrawania, płyny obróbkowe i smary oraz zarządzanie trwałością narzędzi.
1. Prędkości i posuwy:
- A. Prędkość skrawania (prędkość powierzchniowa):Prędkość skrawania, często określana jako prędkość powierzchniowa, to prędkość interakcji przedmiotu obrabianego i narzędzia tnącego. Jest mierzona w stopach powierzchniowych na minutę (SFM) lub metrach na minutę (m/min). Aby zoptymalizować prędkość skrawania, należy wziąć pod uwagę obrabiany materiał i materiał narzędzia. Narzędzia ze stali szybkotnącej (HSS) mają niższe zalecane prędkości skrawania niż na przykład narzędzia z węglików spiekanych. Aby określić zalecane prędkości skrawania dla określonych materiałów i narzędzi, należy zapoznać się z danymi producenta narzędzi lub podręcznikami obróbki.
- B. Szybkość podawania:Szybkość posuwu to prędkość liniowa, z jaką narzędzie tnące wnika w przedmiot obrabiany. Jest mierzony w calach na obrót (IPR) lub milimetrach na obrót (mm/obr). Aby zoptymalizować prędkość posuwu, należy wziąć pod uwagę takie czynniki, jak właściwości materiału, geometria narzędzia i pożądane wykończenie powierzchni. Wyższe szybkości posuwu są na ogół bardziej produktywne, ale mogą wymagać solidniejszego oprzyrządowania.
- C. Zależność prędkości skrawania i posuwu:Zrównoważenie prędkości skrawania i posuwu ma kluczowe znaczenie dla wydajnego usuwania materiału. Zwiększenie prędkości skrawania zazwyczaj pozwala na wyższą prędkość posuwu, ale należy je razem wyregulować, aby zapobiec zużyciu i przegrzaniu narzędzia.
2. Głębokość cięcia:
- A. Głębokość skrawania (DOC):Głębokość skrawania to odległość, na jaką narzędzie tnące wchodzi w obrabiany przedmiot. Należy koniecznie wziąć pod uwagę materiał i możliwości narzędzia. Zoptymalizuj głębokość skrawania w oparciu o twardość materiału oraz wytrzymałość i sztywność narzędzia. Płytkie cięcia mogą być konieczne w przypadku twardszych materiałów, natomiast głębsze cięcia można uzyskać w przypadku miękkich materiałów.
- B. Osiowa i promieniowa głębokość skrawania:Podczas toczenia CNC należy wziąć pod uwagę zarówno osiową (wzdłuż długości przedmiotu obrabianego), jak i promieniową (w poprzek średnicy przedmiotu obrabianego) głębokość skrawania. Optymalne głębokości dla każdego z nich będą się różnić w zależności od operacji i materiału.
3. Płyny do cięcia i smary:
- A. Wybór odpowiedniego płynu do cięcia:Płyny obróbkowe są niezbędne do rozpraszania ciepła, zmniejszania tarcia i poprawy ewakuacji wiórów. Wybierz odpowiedni płyn obróbkowy w zależności od materiału i operacji obróbki. W przypadku różnych materiałów preferowane mogą być chłodziwa rozpuszczalne w wodzie, na bazie oleju mineralnego lub chłodziwa syntetyczne.
- B. Właściwa aplikacja:Skutecznie nałóż płyn chłodzący na obszar cięcia, aby zapewnić odpowiednie smarowanie i chłodzenie. Można tego dokonać poprzez chłodzenie zalewowe, systemy mgły lub doprowadzanie chłodziwa przez narzędzie, w zależności od możliwości maszyny.
- C. Monitorowanie i konserwacja:Regularnie monitoruj poziom, stan i zanieczyszczenie płynu chłodzącego, aby zapewnić jego skuteczność. Konserwuj systemy chłodziwa, aby zapobiec problemom, takim jak rozwój i degradacja bakterii.
4. Zarządzanie trwałością narzędzi:
- A. Kontrola i konserwacja narzędzi:Wdrożyć program rutynowej kontroli i konserwacji narzędzi, aby upewnić się, że narzędzia są w dobrym stanie. Tępe lub uszkodzone narzędzia mogą skutkować gorszą jakością obróbki i zmniejszoną żywotnością narzędzia.
- B. Harmonogram wymiany narzędzia:Ustal harmonogram wymiany narzędzi w oparciu o takie czynniki, jak zużycie narzędzia, czas sprawności maszyny i wymagania produkcyjne. Pomaga to zapobiegać nieoczekiwanym awariom narzędzi i utrzymywać stałą jakość obróbki.
- C. Optymalizacja trwałości narzędzia:Niektóre materiały narzędziowe i powłoki zapewniają dłuższą żywotność narzędzia. Rozważ zastosowanie narzędzi o wysokiej wydajności, aby zoptymalizować trwałość narzędzia i skrócić przestoje produkcyjne.
- D. Kontrola wiórów narzędziowych:Skuteczna kontrola wiórów, w tym zastosowanie łamaczy wiórów i odpowiedniej geometrii narzędzia, może wydłużyć trwałość narzędzia poprzez zmniejszenie zużycia powodowanego przez wióry.
Optymalizacja parametrów skrawania w toczeniu CNC jest procesem ciągłym. Znalezienie najlepszych parametrów dla konkretnego zastosowania może wymagać eksperymentowania i dostrajania. Regularnie monitoruj i dostosowuj te parametry, aby zapewnić optymalną wydajność obróbki, trwałość narzędzia i jakość części. Odpowiednio zoptymalizowane parametry skrawania nie tylko poprawiają wydajność obróbki, ale także zmniejszają zużycie narzędzi, a w efekcie koszty produkcji.
Rozwiązywanie typowych problemów związanych z ustawianiem narzędzi
Rozwiązywanie typowych problemów związanych z ustawianiem narzędzi jest podstawową umiejętnością mechaników i operatorów CNC. Zrozumienie i rozwiązanie tych problemów może pomóc w utrzymaniu precyzji i jakości operacji obróbki. Oto kilka typowych problemów z ustawieniem narzędzi i ich rozwiązania:
1. Drganie narzędzia:
Kwestia: Drgania narzędzia powstają, gdy narzędzie skrawające wibruje podczas procesu obróbki, co prowadzi do złego wykończenia powierzchni, zużycia narzędzia i potencjalnego uszkodzenia przedmiotu obrabianego.
Rozwiązanie:
- Zmniejsz prędkość lub zwiększ posuw: Dostosuj parametry skrawania, zmniejszając prędkość skrawania lub zwiększając posuw. Ta zmiana może wytłumić wibracje i zmniejszyć drgania.
- Sprawdź sztywność narzędzia: Upewnij się, że uchwyt narzędzia i narzędzie są prawidłowo zamocowane i że narzędzie nie wystaje zbyt daleko od uchwytu.
- Sprawdź mocowanie przedmiotu obrabianego: Upewnij się, że obrabiany przedmiot jest bezpiecznie zamocowany, aby zapobiec wibracjom związanym z obrabianym przedmiotem.
- Użyj technik tłumienia: Niektóre maszyny są wyposażone w funkcje tłumienia wibracji. Jeśli są dostępne, rozważ ich użycie.
- Wybierz sztywniejsze narzędzie: Bardziej sztywne narzędzie, na przykład z mniejszą liczbą rowków, może pomóc w ograniczeniu drgań.
2. Słabe wykończenie powierzchni:
Kwestia: Słabe wykończenie powierzchni może wynikać z problemów z ustawieniem narzędzia lub parametrami skrawania, co prowadzi do szorstkich lub niespójnych powierzchni przedmiotu obrabianego.
Rozwiązanie:
- Sprawdź geometrię narzędzia: Upewnij się, że geometria narzędzia tnącego jest odpowiednia do operacji. Ostre narzędzie o prawidłowej geometrii ma kluczowe znaczenie dla uzyskania dobrego wykończenia powierzchni.
- Optymalizuj parametry cięcia: Dostosuj prędkość skrawania, posuw i głębokość skrawania, aby znaleźć najlepszą kombinację dla konkretnego materiału i operacji.
- Sprawdź zużycie narzędzia: Sprawdź narzędzie pod kątem oznak zużycia lub uszkodzeń, takich jak odpryski na krawędziach. W razie potrzeby wymień lub przeszlifuj narzędzie.
- Użyj odpowiedniego płynu do cięcia: Właściwe smarowanie i chłodzenie mogą znacząco wpłynąć na wykończenie powierzchni. Używaj płynu chłodzącego odpowiedniego do materiału i operacji.
- Minimalizuj wibracje: Rozwiąż problemy z wibracjami, aby uniknąć tworzenia nieregularności powierzchni.
3. Niedokładności wymiarowe:
Kwestia: Części mogą mieć nieprawidłowe wymiary z powodu źle ustawionego oprzyrządowania lub zużycia narzędzia.
Rozwiązanie:
- Sprawdź konfigurację narzędzia: Sprawdź, czy narzędzie jest prawidłowo ustawione, ma odpowiednią wysokość i jest ustawione w stosunku do obrabianego przedmiotu.
- Kalibracja maszyny: Upewnij się, że maszyna CNC jest prawidłowo skalibrowana i dokładnie interpretuje przesunięcia narzędzi oraz dane narzędzi.
- Dostosuj przesunięcia narzędzi: Popraw wszelkie błędy w przesunięciach narzędzi, dokładnie mierząc narzędzie i wprowadzając odpowiednie wartości przesunięć w sterowaniu CNC.
- Sprawdź zużycie narzędzia: Regularnie sprawdzaj narzędzie tnące pod kątem zużycia i w razie potrzeby wymień je lub przeszlifuj.
4. Problemy z kontrolą wiórów:
Kwestia: Niewłaściwa kontrola wiórów może prowadzić do problemów, takich jak zatykanie wiórów, słabe odprowadzanie wiórów i uszkodzenie przedmiotu obrabianego lub narzędzia.
Rozwiązanie:
- Wybierz odpowiednią geometrię narzędzia: Wybierz narzędzie skrawające z łamaczem wiórów lub geometrią odpowiednią do materiału i operacji.
- Optymalizuj parametry cięcia: Dostosuj posuw, prędkość skrawania i głębokość skrawania, aby zoptymalizować tworzenie i odprowadzanie wiórów.
- Stosuj odpowiednie smarowanie: Właściwe użycie płynów obróbkowych może pomóc w smarowaniu i ułatwieniu ewakuacji wiórów.
- Sprawdź wyrównanie narzędzia i przedmiotu obrabianego: Upewnij się, że narzędzie jest prawidłowo ustawione w stosunku do przedmiotu obrabianego, aby zapobiec problemom związanym z powstawaniem wiórów.
5. Złamanie narzędzia:
Kwestia: Złamanie narzędzia może nastąpić z powodu nadmiernej siły, nieprawidłowego ustawienia narzędzia lub problemów związanych z materiałem.
Rozwiązanie:
- Optymalizuj parametry cięcia: Zmniejsz siły skrawania, dostosowując parametry, takie jak posuw, prędkość skrawania i głębokość skrawania.
- Sprawdź konfigurację narzędzia: Upewnij się, że narzędzie jest bezpiecznie zamontowane w uchwycie i jest prawidłowo ustawione.
- Użyj odpowiedniego materiału narzędzia: Wybierz odpowiedni materiał narzędzia dla konkretnego materiału, który obrabiasz. Na przykład narzędzia węglikowe są lepsze do twardych materiałów.
- Sprawdź zużycie narzędzia: Regularnie sprawdzaj narzędzie pod kątem oznak zużycia i wymieniaj je, zanim stanie się nadmiernie zużyte i podatne na pękanie.
Rozwiązanie tych typowych problemów z ustawieniem narzędzi wymaga połączenia odpowiedniego szkolenia, regularnej konserwacji i systematycznego podejścia do rozwiązywania problemów. Zdolność do diagnozowania i rozwiązywania problemów związanych z narzędziami ma kluczowe znaczenie dla osiągnięcia wysokiej jakości i wydajnych wyników obróbki.
Wnioski w
Proces ustawiania i optymalizacji tokarskich narzędzi skrawających do toczenia CNC jest kluczowym aspektem obróbki, który znacząco wpływa na jakość, wydajność i precyzję procesów produkcyjnych. Dogłębne zrozumienie komponentów i funkcji narzędzi skrawających, a także czynników związanych z wyborem narzędzi, jest niezbędne dla mechaników i operatorów CNC.
Prawidłowe ustawienie narzędzia skrawającego wymaga systematycznego podejścia, począwszy od przygotowania tokarki i przedmiotu obrabianego, po wybór odpowiedniego uchwytu narzędzia, montaż narzędzia, regulację wysokości narzędzia i wyrównania linii środkowej oraz konfigurację kompensacji promienia ostrza narzędzia i przesunięć narzędzia. Każdy krok odgrywa kluczową rolę w osiągnięciu precyzyjnych i wydajnych wyników obróbki.
Optymalizacja parametrów skrawania, w tym prędkości i posuwów, głębokości skrawania, płynów obróbkowych i zarządzania trwałością narzędzi, to kolejny krytyczny aspekt toczenia CNC. Starannie dobierając odpowiednie parametry, mechanicy mogą zwiększyć produktywność, utrzymać trwałość narzędzi i poprawić jakość wykończenia powierzchni.
Wreszcie, możliwość rozwiązywania typowych problemów z ustawieniem narzędzia, takich jak drgania narzędzia, słabe wykończenie powierzchni, niedokładności wymiarowe, problemy z kontrolą wiórów i pękanie narzędzia, jest niezbędna do utrzymania spójnych i wysokiej jakości wyników obróbki. Identyfikacja tych problemów i wdrożenie odpowiednich rozwiązań gwarantuje, że proces obróbki przebiega sprawnie i efektywnie.
Ogólnie rzecz biorąc, wszechstronne zrozumienie narzędzi skrawających tokarki i ich konfiguracji, w połączeniu z możliwością optymalizacji parametrów skrawania i rozwiązywania problemów, umożliwia mechanikom osiąganie najlepszych wyników w operacjach toczenia CNC. Ciągłe uczenie się, szkolenia i doświadczenie są kluczem do doskonalenia tych umiejętności i zapewnienia pomyślnych procesów obróbki.
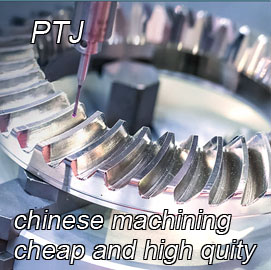
- Obróbka 5-osiowa
- Frezowanie CNC
- Toczenie CNC
- Obróbka przemysłowa
- Proces obróbki
- Obróbka powierzchniowa
- Obróbka metali
- Obróbka tworzyw sztucznych
- Formy do metalurgii proszków
- Die Casting
- Galeria części
- Auto części metalowe
- Części maszynerii
- Radiator LED
- Części budowlane
- Części mobilne
- Części medyczne
- Części elektroniczne
- Obróbka na miarę
- Części rowerowe
- Obróbka aluminium
- Obróbka tytanu
- Obróbka stali nierdzewnej
- Obróbka miedzi
- Obróbka mosiądzu
- Obróbka super stopów
- Obróbka podglądowa
- Obróbka UHMW
- Jednolita obróbka
- Obróbka PA6
- Obróbka PPS
- Obróbka teflonowa
- Obróbka Inconelu
- Obróbka stali narzędziowej
- Więcej materiału