Jak prawidłowo montować i instalować obrabiarki CNC oraz dobre wskazówki
2023-10-30
Rozdział 1: Zrozumienie maszyn CNC
W tym rozdziale położymy podstawy, badając, czym są maszyny CNC, różne dostępne typy i kluczowe komponenty tworzące maszynę CNC.A. Co to jest maszyna CNC?
Maszyna CNC, skrót od Computer Numerical Control machine, to wyrafinowany sprzęt używany w produkcji i proces obróbkies. W przeciwieństwie do konwencjonalnych maszyn obsługiwanych ręcznie przez człowieka, maszyny CNC są zautomatyzowane i kontrolowane przez komputery, co pozwala na precyzyjne i wysoce powtarzalne operacje. Maszyny te są w stanie wykonywać złożone zadania, takie jak cięcie, wiercenie, frezowanie i kształtowanie materiałów, takich jak metal, plastik, drewno i inne. Sercem maszyny CNC jest jej zdolność do interpretowania i wykonywania poleceń z oprogramowania do projektowania wspomaganego komputerowo (CAD) lub produkcji wspomaganej komputerowo (CAM). Oprogramowanie to generuje serię kodów numerycznych, często nazywanych kodami G i kodami M, które instruują maszynę CNC, jak przesuwać narzędzia skrawające i przedmiot obrabiany, aby osiągnąć pożądany rezultat. Maszyny CNC zrewolucjonizowały przemysł produkcyjny, zwiększając wydajność, ograniczając błędy ludzkie i umożliwiając produkcję skomplikowanych i niestandardowych komponentów.B. Rodzaje maszyn CNC
Maszyny CNC są dostępne w różnych typach, każdy przeznaczony do konkretnych zastosowań i branż. Oto kilka popularnych typów maszyn CNC:- Frezowanie CNC maszyny: Maszyny te służą do cięcia i kształtowania materiałów za pomocą obrotowych narzędzi skrawających. Są szeroko stosowane w takich gałęziach przemysłu, jak przemysł lotniczy, motoryzacyjny i obróbka metali, do zadań takich jak wiercenie, frezowanie i grawerowanie.
- Tokarki CNC: Tokarki CNC są przeznaczone do obracania przedmiotu obrabianego, podczas gdy narzędzie skrawające służy do usuwania z niego materiału. Są niezbędne do produkcji elementów cylindrycznych, takich jak wałsi tulejas.
- Routery CNC: Maszyny te są używane głównie do cięcia i kształtowania materiałów, takich jak drewno, tworzywa sztuczne i kompozyty. Routery CNC są powszechne w przemyśle drzewnym i przy produkcji znaków.
- Przecinarki plazmowe CNC: Idealne do cięcia blach, przecinarki plazmowe CNC wykorzystują strumień zjonizowanego gazu o dużej prędkości do topienia i usuwania materiału. Zatrudnieni są w przemyśle metalowym i motoryzacyjnym.
- Wycinarki laserowe CNC: Maszyny do cięcia laserowego wykorzystują wiązkę lasera o dużej mocy do precyzyjnego cięcia lub grawerowania różnych materiałów, w tym metali, tworzyw sztucznych i tekstyliów. Znajdują zastosowanie w różnych gałęziach przemysłu, od wyrobu biżuterii po produkcję przemysłową.
- Przecinarki wodne CNC: Przecinarki wodne wykorzystują strumień wody pod wysokim ciśnieniem zmieszany z cząsteczkami ściernymi do przecinania materiałów. Nadają się do cięcia szerokiej gamy materiałów, w tym kamienia, szkła i metali.
- Maszyny CNC EDM: Maszyny do obróbki elektroerozyjnej (EDM) wykorzystują wyładowania elektryczne do erodowania materiału z przedmiotu obrabianego. Stosowane są do skomplikowanych i precyzyjnych zadań, zwłaszcza przy budowie narzędzi i matryc.
C. Elementy maszyny CNC
Zrozumienie elementów maszyny CNC ma kluczowe znaczenie dla skutecznej obsługi i konserwacji. Oto kluczowe elementy znajdujące się w większości maszyn CNC:- Rama maszyny: Rama maszyny stanowi podporę konstrukcyjną dla całej maszyny CNC. Zwykle jest wykonany z wytrzymałych materiałów, aby zapewnić stabilność i sztywność podczas pracy.
- Wrzeciono: Wrzeciono to napędzany silnikiem element odpowiedzialny za przytrzymywanie i obracanie narzędzi skrawających lub osprzętu. Odgrywa kluczową rolę w precyzji i szybkości procesu obróbki.
- System osi: Maszyny CNC działają wzdłuż wielu osi, zwykle oznaczonych jako X, Y i Z. Osie te definiują ruch maszyny w przestrzeni trójwymiarowej. Niektóre maszyny mogą mieć dodatkowe osie obrotowe, takie jak A, B i C, w przypadku bardziej złożonych operacji.
- Zmieniacz narzędzi: Wiele maszyn CNC wyposażonych jest w automatyczne zmieniacze narzędzi, które pozwalają na szybką zmianę narzędzi skrawających w trakcie procesu obróbki. Poprawia to wydajność i skraca przestoje.
- Panel sterowania: Panel sterowania zawiera interfejs, za pośrednictwem którego operatorzy lub programiści mogą wprowadzać polecenia, ładować programy i monitorować stan maszyny.
- Stół roboczy lub system mocowania: Stół roboczy to miejsce, na którym przedmiot obrabiany jest bezpiecznie utrzymywany na miejscu podczas obróbki. Różne urządzenia do mocowania, takie jak zaciski, imadła i armatura, służą do zapewnienia stabilności i prawidłowego ustawienia przedmiotu obrabianego.
- System napędowy: Układ napędowy stanowią silniki i siłowniki odpowiedzialne za przemieszczanie elementów maszyny po zadanych osiach. Precyzyjne sterowanie układem napędowym jest niezbędne do dokładnej obróbki.
- Układ chłodzenia: Chłodzenie jest niezbędne podczas Wieloosiowa obróbka CNC aby zapobiec przegrzaniu narzędzi i przedmiotów obrabianych. Maszyny CNC często są wyposażone w układ chłodziwa w celu utrzymania optymalnej temperatury.
- Komputer sterujący: Komputer sterujący zawiera sprzęt i oprogramowanie niezbędne do obsługi maszyny CNC. Interpretuje kody G i kody M generowane przez oprogramowanie CAD/CAM i przekształca je w ruchy i działania.
Rozdział 2: Przygotowanie przed instalacją
Zanim przystąpisz do instalacji maszyny CNC, bardzo ważne jest dokonanie dokładnych przygotowań. W tym rozdziale opisano istotne kwestie przed instalacją, w tym konfigurację przestrzeni roboczej, wymagania dotyczące zasilania i instalacji elektrycznej oraz środki bezpieczeństwa zapewniające płynny i bezpieczny proces instalacji.A. Rozważania dotyczące obszaru roboczego
- Wymagania dotyczące miejsca: Zacznij od oceny dostępnej przestrzeni w warsztacie lub obiekcie. Upewnij się, że obszar jest wystarczająco przestronny, aby pomieścić maszynę CNC, w tym wystarczającą ilość miejsca na bezpieczny dostęp i konserwację. Należy wziąć pod uwagę wymiary maszyny, przestrzeń wymaganą do przenoszenia materiałów oraz wszelkie dodatkowe wyposażenie lub stanowiska robocze.
- wentylacja: Odpowiednia wentylacja ma kluczowe znaczenie dla rozproszenia ciepła powstającego podczas obróbki i usunięcia wszelkich potencjalnie szkodliwych oparów i cząstek pyłu. Zainstaluj odpowiednie systemy wentylacji lub sprzęt do filtrowania powietrza, jeśli jest to konieczne, aby utrzymać czyste i bezpieczne środowisko pracy.
- Podłogi: Upewnij się, że podłoga w wyznaczonym miejscu jest równa, stabilna i wytrzymuje ciężar maszyny CNC. Nierówne lub słabe podłoże może prowadzić do wibracji maszyny i niedokładności podczas pracy.
- Dostępność: Zaplanuj łatwy dostęp do maszyny CNC na potrzeby instalacji, konserwacji i naprawy. Upewnij się, że są czyste ścieżki i wystarczająca przestrzeń do manewrowania ciężkimi maszynami i materiałami.
- Oświetlenie: Odpowiednie oświetlenie jest niezbędne do bezpiecznej i dokładnej pracy. Upewnij się, że miejsce pracy jest dobrze oświetlone, aby zapobiec wypadkom i zapewnić dobrą widoczność procesu obróbki.
B. Wymagania dotyczące zasilania i prądu
- Dostawy prądu: Określ konkretne wymagania elektryczne swojej maszyny CNC. Sprawdź specyfikacje techniczne maszyny i skonsultuj się z producentem lub dostawcą, aby upewnić się, że zasilanie elektryczne Twojego zakładu spełnia te wymagania.
- Napięcie i faza: Maszyny CNC mogą wymagać różnych poziomów napięcia (np. 110 V, 220 V, 440 V) i faz (jednofazowe lub trójfazowe). Upewnij się, że zasilanie elektryczne odpowiada specyfikacjom urządzenia.
- Panel elektryczny: Zainstaluj dedykowany panel elektryczny dla maszyny CNC, aby zapobiec przeciążeniu istniejących obwodów. Zatrudnij licencjonowanego elektryka, aby profesjonalnie zajął się okablowaniem i połączeniami.
- Ochrona przed przepięciami: Zainwestuj w urządzenia przeciwprzepięciowe, aby chronić wrażliwe elementy elektroniczne maszyny CNC przed wahaniami napięcia i przepięciami elektrycznymi.
- Grunt: Zapewnij właściwe uziemienie zarówno maszyny CNC, jak i układu elektrycznego, aby zmniejszyć ryzyko zagrożeń elektrycznych i uszkodzenia sprzętu.
C. Środki bezpieczeństwa
- Sprzęt bezpieczeństwa: Nadaj priorytet bezpieczeństwu, zapewniając operatorom i technikom odpowiednie środki ochrony osobistej (PPE). Może to obejmować okulary ochronne, ochronniki słuchu, rękawice i odzież ochronną.
- Procedury awaryjne: Opracuj i udokumentuj procedury awaryjnego wyłączania, które mogą szybko zatrzymać maszynę CNC w przypadku nieprzewidzianych zdarzeń lub wypadków. Należy upewnić się, że cały personel został przeszkolony w zakresie tych procedur.
- Bezpieczeństwo przeciwpożarowe: Zainstaluj gaśnice i czujniki dymu w pobliżu maszyny CNC. Wdrożyć protokoły bezpieczeństwa przeciwpożarowego, takie jak trzymanie materiałów łatwopalnych z dala od maszyny i przestrzeganie planu wyjścia pożarowego.
- Blokada/Tagout (LOTO): Wdrożyć procedury LOTO, aby zapobiec przypadkowemu uruchomieniu maszyny podczas konserwacji lub naprawy. Używaj zamków i przywieszek, aby wskazać, kiedy maszyna jest w trakcie serwisowania.
- Trening bezpieczeństwa: Przeprowadź kompleksowe szkolenie w zakresie bezpieczeństwa dla całego personelu, który będzie obsługiwać, konserwować lub pracować przy maszynie CNC. Podkreśl bezpieczne praktyki i znaczenie przestrzegania protokołów bezpieczeństwa.
- Pierwsza pomoc: Trzymaj dobrze zaopatrzoną apteczkę w pobliżu maszyny CNC. Należy upewnić się, że w przypadku obrażeń dostępny jest przeszkolony personel, który będzie w stanie udzielić natychmiastowej pierwszej pomocy.
Rozdział 3: Montaż maszyny CNC
Kiedy już zakończysz przygotowania przedmontażowe, czas przejść do fazy montażu. W tym rozdziale przedstawimy przewodnik krok po kroku dotyczący montażu maszyny CNC, obejmujący podstawowe zadania, od rozpakowania i kontroli po uporządkowanie kabli.A. Rozpakowanie i kontrola
- unboxing: Rozpocznij od ostrożnego rozpakowania wszystkich elementów maszyny CNC. Postępuj zgodnie z instrukcjami producenta dotyczącymi rozpakowywania, aby uniknąć uszkodzeń w trakcie procesu. W razie potrzeby użyj odpowiednich narzędzi i sprzętu do podnoszenia.
- Zapas komponentów: Utwórz listę kontrolną zapasów, aby upewnić się, że otrzymałeś wszystkie komponenty wymienione w instrukcji obsługi lub dokumentacji maszyny. Sprawdź, czy niczego nie brakuje lub nie jest uszkodzone.
- Sprawdź pod kątem uszkodzeń: Dokładnie sprawdź każdy element pod kątem oznak uszkodzeń, takich jak wgniecenia, zadrapania lub wygięte części. Udokumentuj wszelkie problemy i natychmiast powiadom producenta lub dostawcę.
B. Organizowanie komponentów
- Zorganizuj obszar pracy: Przed montażem upewnij się, że miejsce pracy jest czyste i dobrze zorganizowane. Usuń bałagan i zapewnij wystarczająco dużo miejsca na rozmieszczenie i uporządkowanie komponentów.
- Grupuj podobne części: Pogrupuj podobne części, aby ułatwić proces montażu. Komponenty takie jak łącznikwsporniki i okucia należy umieścić w oddzielnych pojemnikach lub tacach, aby zapewnić łatwy dostęp.
- Zapoznaj się z podręcznikami: Zapoznaj się z instrukcjami montażu i dokumentacją dostarczoną przez producenta. Zapoznaj się z etapami montażu, schematami i wszelkimi szczegółowymi instrukcjami.
C. Montaż ramy maszyny
- Zespół podstawy: Zacznij od podstawy maszyny CNC. Postępuj zgodnie z instrukcjami producenta, aby bezpiecznie zamontować ramę podstawy. Upewnij się, że jest wypoziomowany i stabilny.
- Konstrukcje kolumnowe i wsporcze: Zmontuj kolumny i konstrukcje wsporcze, dopasowując je dokładnie do podstawy. Dokręcić wszystkie śruby i elementy mocujące zalecanym momentem obrotowym.
- Prowadnice i szyny: Zamontuj prowadnice i szyny, które będą kierować ruchem elementów tnących lub utrzymujących narzędzie maszyny. Upewnij się, że są odpowiednio wyrównane i bezpiecznie przymocowane.
D. Mocowanie silników i napędów
- Instalacja silnika: Zamontuj silniki w wyznaczonych miejscach, zgodnie z instrukcjami producenta. Upewnij się, że silniki są bezpiecznie zamocowane i dopasowane do mechanizmów napędowych.
- System napędowy: Silniki połączyć z mechanizmami napędowymi za pomocą odpowiednich sprzęgieł lub pasów. Zapewnij odpowiednie napięcie i wyrównanie, aby zapobiec luzom i niedokładnościom.
mi. Instalowanie Panelu Sterowania
- Montaż panelu sterowania: Zainstaluj panel sterowania w dogodnym miejscu, zwykle w zasięgu operatora. Upewnij się, że jest bezpiecznie zamontowany i ustawiony tak, aby zapewnić optymalną widoczność i dostępność.
- Połączenia elektryczne: Podłączyć panel sterujący do instalacji elektrycznej maszyny zgodnie ze schematami elektrycznymi zawartymi w dokumentacji producenta. Dokładnie sprawdź wszystkie połączenia pod kątem dokładności.
F. Zarządzanie kablami
- Prowadzenie kabli: Ostrożnie poprowadź wszystkie kable, przewody i węże w zorganizowany sposób, aby zapobiec splątaniu lub kolizji z ruchomymi częściami. Do mocowania i ochrony kabli należy używać korytek kablowych lub zacisków.
- Oznakowanie: Oznacz kable i przewody znacznikami identyfikacyjnymi lub przywieszkami, aby uprościć rozwiązywanie problemów i konserwację. Wyraźnie oznacz przeznaczenie i przeznaczenie każdego kabla.
- Testowanie: Przed zamknięciem jakichkolwiek obudów lub paneli należy przeprowadzić wstępny test, aby upewnić się, że wszystkie połączenia elektryczne działają prawidłowo. Sprawdź, czy silniki i czujniki reagują zgodnie z oczekiwaniami.
Rozdział 4: Wyrównywanie i poziomowanie
W rozdziale 4 zagłębimy się w krytyczny proces wyrównywania i poziomowania maszyny CNC. Prawidłowe ustawienie i wypoziomowanie ma fundamentalne znaczenie dla zapewnienia dokładności i precyzji operacji maszyny. W tym rozdziale omówiono znaczenie wyrównywania i poziomowania, potrzebne narzędzia i sprzęt oraz przewodnik krok po kroku dotyczący procesu wyrównywania i poziomowania.A. Znaczenie wyrównania i poziomowania
- Dokładność i precyzja: Wyrównanie i wypoziomowanie są niezbędne do osiągnięcia wysokiego stopnia dokładności i precyzji wymaganego w obróbce CNC. Niewspółosiowość lub nierówności mogą prowadzić do błędów wymiarowych gotowych detali.
- Mniejsze zużycie: Właściwe ustawienie zmniejsza niepotrzebne obciążenie elementów maszyny, takich jak Łożyskoi prowadnice. Wydłuża to żywotność maszyny i zmniejsza koszty konserwacji.
- Zminimalizowane wibracje: Dobrze ustawiona i wypoziomowana maszyna generuje mniej wibracji, co skutkuje lepszym wykończeniem powierzchni i mniejszym zużyciem narzędzi. Wibracje mogą również wpływać na trwałość wrażliwych elementów elektronicznych.
- Bezpieczeństwo: Nieprawidłowo ustawione lub nierówne maszyny mogą stwarzać zagrożenie dla bezpieczeństwa. Na przykład maszyna, która nie jest wypoziomowana, może się przewrócić lub nieoczekiwanie poruszyć podczas pracy.
B. Potrzebne narzędzia i sprzęt
Aby prawidłowo wykonać wyrównywanie i poziomowanie, potrzebne będą następujące narzędzia i sprzęt:- Poziomy precyzji: Precyzyjne niwelatory wysokiej jakości mają kluczowe znaczenie dla dokładnego pomiaru ustawienia i wypoziomowania maszyny.
- Narzędzia do regulacji: W zależności od konstrukcji maszyny mogą być potrzebne określone narzędzia, takie jak klucze, podkładki regulacyjne lub śruby regulacyjne.
- Wskaźniki zegarowe: Czujniki zegarowe pomagają w pomiarze współosiowości różnych elementów maszyny, w tym wrzeciona narzędzia i stołu roboczego.
- Wskaźniki szczelinowe: Szczelinomierze służą do pomiaru szczelin i luzów pomiędzy elementami maszyny podczas osiowania.
- Laser wyrównujący: Laser wyrównujący może być przydatny do oceny prostoliniowości prowadnic i innych elementów liniowych.
C. Proces wyrównywania i poziomowania krok po kroku
Wykonaj poniższe kroki, aby wyrównać i wypoziomować maszynę CNC:Krok 1: Przygotuj przestrzeń roboczą
Upewnij się, że miejsce pracy jest czyste, wolne od zanieczyszczeń i dobrze oświetlone. Usuń wszelkie przeszkody, które mogą utrudniać proces wyrównywania i poziomowania.Krok 2: Ustalenie punktu odniesienia
Wybierz stabilny punkt odniesienia na ramie lub podstawie maszyny, zwykle zapewniany przez producenta. Punkt ten będzie punktem odniesienia dla wszystkich pomiarów.Krok 3: Wypoziomuj maszynę
- Umieść precyzyjne poziomice na różnych powierzchniach maszyny, takich jak podstawa, kolumny i stół roboczy.
- W razie potrzeby wyreguluj śruby poziomujące lub podkładki, aby uzyskać idealne wyrównanie w poziomie. Sprawdź precyzję wskaźników bąbelków na poziomach.
Krok 4: Wyrównanie prowadnic i prowadnic
- Użyj czujników zegarowych i laserów wyrównujących, aby sprawdzić prostoliniowość i równoległość prowadnic, prowadnic i innych elementów liniowych.
- Wyreguluj odpowiednie komponenty, aby skorygować wykrytą niewspółosiowość.
Krok 5: Wyrównanie wrzeciona
- Zamontuj czujnik zegarowy na wrzecionie maszyny lub uchwycie narzędziowym.
- Obróć wrzeciono, aby sprawdzić bicie i koncentryczność. W razie potrzeby wyreguluj wrzeciono, aby zminimalizować bicie.
Krok 6: Wyrównanie stołu roboczego
- Sprawdź ustawienie stołu roboczego lub uchwytu roboczego za pomocą czujników zegarowych.
- Dostosuj położenie stołu roboczego, aby upewnić się, że jest on prostopadły do osi maszyny.
- Po regulacji sprawdź ponownie wszystkie wyrównania, aby upewnić się, że spełniają określone tolerancje.
- Przeprowadzić przebiegi testowe, aby sprawdzić, czy maszyna działa dokładnie i daje pożądane wyniki.
Krok 8: Dokumentacja
Prowadź szczegółowe zapisy procesu wyrównywania i poziomowania, w tym pomiary, dokonane regulacje i wszelkie napotkane problemy. Dokumentacja ta będzie cenna do wykorzystania w przyszłości i konserwacji.Krok 9: Kontrola końcowa i certyfikacja
Rozważ zlecenie wykwalifikowanemu technikowi lub inżynierowi przeprowadzenia kontroli końcowej i certyfikacji, aby upewnić się, że maszyna CNC spełnia standardy branżowe i wymagania bezpieczeństwa. Prawidłowe ustawienie i wypoziomowanie są niezbędne do niezawodnego i dokładnego działania maszyny CNC. Nie spiesz się podczas tego procesu, ponieważ precyzja jest najważniejsza. Wykonując poniższe kroki i korzystając z odpowiednich narzędzi, możesz mieć pewność, że Twoja maszyna jest w optymalnym stanie, umożliwiającym pomyślną obróbkę. W następnym rozdziale omówimy wymagania dotyczące okablowania elektrycznego maszyny CNC.Rozdział 5: Okablowanie elektryczne
W tym rozdziale zajmiemy się aspektami okablowania elektrycznego instalacji maszyny CNC. Prawidłowe okablowanie elektryczne ma kluczowe znaczenie dla bezpiecznej i wydajnej pracy maszyny. W tym rozdziale opisano zrozumienie układów elektrycznych, okablowanie maszyny CNC i ważne środki ostrożności.A. Zrozumienie systemów elektrycznych
- Zasilanie: Maszyny CNC wymagają stabilnego i odpowiedniego zasilania. Zapoznaj się z wymaganiami dotyczącymi napięcia, częstotliwości i fazy określonymi przez producenta maszyny. Upewnij się, że źródło zasilania jest niezawodne i ma odpowiednią wydajność, aby obsłużyć obciążenie elektryczne maszyny.
- Panel elektryczny: Większość maszyn CNC ma panel elektryczny, w którym znajdują się różne komponenty, w tym wyłączniki automatyczne, przekaźniki, styczniki i listwy zaciskowe. Zapoznaj się z elementami panelu i ich funkcjami.
- Schematy połączeń: Przejrzyj schematy połączeń dostarczone przez producenta maszyny. Schematy te ilustrują połączenia pomiędzy komponentami i są niezbędne do prawidłowego okablowania.
- Grunt: Prawidłowe uziemienie ma kluczowe znaczenie dla bezpieczeństwa. Upewnij się, że maszyna i instalacja elektryczna są uziemione zgodnie z lokalnymi przepisami elektrycznymi i zaleceniami producenta.
B. Okablowanie maszyny CNC
Wykonaj poniższe kroki, aby okablować maszynę CNC:Krok 1: Wyłącz
Przed rozpoczęciem jakichkolwiek prac związanych z okablowaniem należy upewnić się, że maszyna i źródło zasilania są wyłączone. Odłącz maszynę od źródła zasilania.Krok 2: Plan okablowania
Utwórz plan okablowania w oparciu o schematy okablowania producenta. Zidentyfikuj komponenty, takie jak silniki, czujniki, przełączniki i panel sterowania, oraz określ ich wzajemne połączenia.Krok 3: Wybór kabla
Używaj odpowiednich kabli i przewodów, które spełniają wymagania dotyczące napięcia i prądu maszyny. Upewnij się, że kable mają odpowiedni przekrój i typ izolacji.Krok 4: Prowadzenie kabli
Ostrożnie poprowadź kable i przewody wzdłuż korytek lub kanałów kablowych maszyny. Utrzymuj je w porządku i oddziel od ruchomych elementów, aby zapobiec uszkodzeniom.Krok 5: Połączenia terminalowe
Podłącz przewody do odpowiednich zacisków na komponentach, takich jak silniki, czujniki i przełączniki. W razie potrzeby należy zapewnić bezpieczne połączenia poprzez zaciskanie lub lutowanie. Aby ułatwić identyfikację, użyj etykiet przewodów.Krok 6: Okablowanie panelu sterowania
Wewnątrz panelu sterowania podłącz przewody do odpowiednich listew zaciskowych, wyłączników automatycznych, styczników i przekaźników zgodnie ze schematami połączeń. Podczas swojej pracy należy zachować szczególną ostrożność, aby uniknąć połączeń krzyżowych lub luźnych przewodów.Krok 7: Podłączenie zasilania
Podłącz maszynę do źródła zasilania zgodnie z wytycznymi producenta. Dokładnie sprawdź ustawienia napięcia, fazy i częstotliwości, aby upewnić się, że odpowiadają wymaganiom urządzenia.Krok 8: Środki bezpieczeństwa
W razie potrzeby należy wdrożyć funkcje bezpieczeństwa, takie jak wyłączniki awaryjne i blokady bezpieczeństwa. Upewnij się, że te urządzenia zabezpieczające są prawidłowo okablowane i przetestowane pod kątem funkcjonalności.Krok 9: Testowanie
Przed zamknięciem panelu sterowania i włączeniem zasilania maszyny należy wykonać test ciągłości, aby sprawdzić, czy nie ma uszkodzeń okablowania lub zwarć. Upewnij się, że wszystkie połączenia są pewne i wolne od luźnych żył.C. Środki ostrożności
- Blokada/Tagout (LOTO): Wdrożyć procedury LOTO, aby zapobiec przypadkowemu uruchomieniu maszyny podczas okablowania lub czynności konserwacyjnych. Do izolowania źródeł zasilania należy stosować urządzenia blokujące.
- Wykwalifikowany elektryk: Prace elektryczne powinny być wykonywane przez wykwalifikowanego elektryka lub technika posiadającego wiedzę na temat wymagań elektrycznych maszyny i lokalnych przepisów elektrycznych.
- Ochrona przed przeładowaniem: Zainstaluj odpowiednie urządzenia zabezpieczające przed przeciążeniem, takie jak wyłączniki automatyczne lub bezpieczniki, aby zapobiec uszkodzeniom w przypadku usterek elektrycznych.
- Grunt: Upewnij się, że maszyna i wszystkie komponenty elektryczne są prawidłowo uziemione, aby zapobiec zagrożeniom elektrycznym.
- Oznakowanie: Wyraźnie oznacz wszystkie przewody, kable i komponenty, aby ułatwić rozwiązywanie problemów i przyszłą konserwację.
- Regularne kontrole: Okresowo sprawdzaj układ elektryczny pod kątem oznak zużycia, uszkodzeń lub poluzowanych połączeń. Natychmiast rozwiązuj wszelkie problemy.
- Procedury awaryjne: Ustanawianie i komunikowanie procedur awaryjnych w przypadku problemów z elektryką, w tym pożarów elektrycznych lub porażenia prądem elektrycznym.
Rozdział 6: Instalacja oprogramowania sterującego
W tym rozdziale omówimy proces instalacji oprogramowania sterującego dla Twojej maszyny CNC. Oprogramowanie sterujące to mózg systemu CNC, odpowiedzialny za interpretację i wykonanie instrukcji obróbki. W tym rozdziale opisano przegląd oprogramowania sterującego maszyną CNC, przewodnik krok po kroku dotyczący instalacji oprogramowania oraz procedury kalibracji i testowania.A. Przegląd oprogramowania do sterowania maszynami CNC
- Rola oprogramowania sterującego: Oprogramowanie sterujące maszyną CNC odpowiada za tłumaczenie danych projektowych i ścieżek narzędzia z oprogramowania CAD/CAM na określone ruchy maszyny. Generuje kody G i M, które sterują silnikami i siłownikami maszyny.
- Rodzaje oprogramowania sterującego: Istnieją różne rodzaje oprogramowania sterującego CNC, począwszy od zastrzeżonego oprogramowania dostarczanego przez producentów maszyn po rozwiązania typu open source i rozwiązania innych firm. Wybierz oprogramowanie, które odpowiada wymaganiom Twojej maszyny i Twojej znajomości jej interfejsu.
- Cechy: Oprogramowanie sterujące może się różnić pod względem funkcji i możliwości. Poszukaj oprogramowania oferującego funkcje niezbędne do spełnienia konkretnych potrzeb w zakresie obróbki, takie jak generowanie ścieżki narzędzia, wymiana narzędzi i kontrola prędkości wrzeciona.
B. Instalacja oprogramowania krok po kroku
Wykonaj poniższe kroki, aby zainstalować oprogramowanie sterujące dla swojej maszyny CNC:Krok 1: Wymagania systemowe
Sprawdź wymagania systemowe określone przez producenta oprogramowania sterującego. Upewnij się, że komputer spełnia te wymagania pod względem sprzętu, systemu operacyjnego i dostępnej pamięci.Krok 2: Pobieranie oprogramowania lub nośnik instalacyjny
Oprogramowanie sterujące pozyskaj pobierając je ze strony internetowej producenta lub korzystając z nośnika instalacyjnego dostarczonego przez producenta.Krok 3: instalacja
- Kliknij dwukrotnie plik instalacyjny oprogramowania, aby rozpocząć proces instalacji.
- Postępuj zgodnie z instrukcjami wyświetlanymi na ekranie przez instalatora. Może to obejmować wybranie katalogów instalacyjnych, zaakceptowanie umów licencyjnych i skonfigurowanie ustawień oprogramowania.
- Upewnij się, że instalacja przebiegła pomyślnie i nie napotkano żadnych błędów.
Krok 4: Licencjonowanie i aktywacja
Jeżeli oprogramowanie sterujące wymaga licencji lub aktywacji, należy postępować zgodnie ze wskazówkami producenta, aby dokończyć ten proces. Upewnij się, że masz niezbędne klucze licencyjne lub kody aktywacyjne.Krok 5: Konfiguracja maszyny
Skonfiguruj oprogramowanie sterujące tak, aby odpowiadało specyfikacjom Twojej maszyny CNC. Może to obejmować ustawienie parametrów osi maszyny, typów silników i innych komponentów sprzętowych.Krok 6: Baza danych narzędzi i materiałów
Utwórz lub zaimportuj bazę danych narzędzi i materiałów do oprogramowania sterującego. Informacja ta jest kluczowa dla wygenerowania ścieżki narzędzia i doboru odpowiednich parametrów obróbki.C. Kalibracja i testowanie
Po zainstalowaniu oprogramowania sterującego wykonaj następujące kroki w celu kalibracji i testowania:Krok 1: Ustawienie bazowania i punktu odniesienia
- Ustaw maszynę w pozycji wyjściowej, przesuwając wszystkie osie do pozycji odniesienia lub pozycji wyjściowej. Ustala to znany punkt początkowy ruchów maszyny.
- Sprawdź, czy maszyna dokładnie powraca do pozycji referencyjnej.
Krok 2: Kalibracja narzędzia
- Kalibracja długości i średnicy narzędzia. Dzięki temu maszyna zna dokładne wymiary narzędzi, których będzie używać.
- Wykonaj cięcia testowe lub procedury styku narzędzia, aby sprawdzić kalibrację narzędzia.
Krok 3: Konfiguracja przedmiotu obrabianego
- Zamocuj testowany przedmiot lub materiał na stole roboczym lub systemie mocowania maszyny.
- Upewnij się, że obrabiany przedmiot jest prawidłowo ustawiony i zabezpieczony.
Krok 4: Uruchomienia testowe
- Załaduj prosty program testowy do oprogramowania sterującego.
- Uruchom program testowy, aby obserwować ruchy maszyny i wyniki obróbki.
- Sprawdź, czy nie występują problemy, takie jak nieoczekiwane ruchy, kolizje narzędzi lub niedokładności.
Krok 5: Dostrajanie
Jeśli podczas testowania zostaną zidentyfikowane problemy, w razie potrzeby dostosuj ustawienia oprogramowania sterującego, korekcje narzędzi lub konfigurację przedmiotu obrabianego. Powtarzaj przebiegi testowe, aż maszyna będzie działać dokładnie i niezawodnie.Krok 6: Dokumentacja
Dokumentuj wszystkie wyniki kalibracji i testów, w tym wszelkie regulacje wprowadzone w oprogramowaniu sterującym. Niniejsza dokumentacja jest cenna do wykorzystania w przyszłości i rozwiązywania problemów. Instalacja oprogramowania sterującego jest kluczowym krokiem w procesie konfiguracji maszyny CNC. Postępując zgodnie z instrukcjami producenta, kalibrując maszynę i przeprowadzając dokładne testy, możesz mieć pewność, że Twoja maszyna CNC jest gotowa do produkcji i zdolna do wytwarzania precyzyjnych i dokładnych wyników. W następnym rozdziale zbadamy znaczenie smarowania i konserwacji dla utrzymania wydajności i trwałości maszyny CNC.Rozdział 7: Smarowanie i konserwacja
W tym rozdziale skupimy się na krytycznych aspektach smarowania i konserwacji maszyny CNC. Właściwe smarowanie i regularna konserwacja są niezbędne do zapewnienia trwałości, dokładności i niezawodności sprzętu CNC. Omówimy znaczenie smarowania, punktów smarowania i ustalenia harmonogramu konserwacji.A. Dlaczego smarowanie jest ważne
Smarowanie odgrywa kluczową rolę w wydajności i trwałości maszyny CNC z kilku powodów:- Redukcja tarcia: Smarowanie zmniejsza tarcie pomiędzy ruchomymi częściami, takimi jak łożyska, prowadnice i śruby kulowe. Minimalizuje to zużycie podzespołów i wydłuża ich żywotność.
- Rozpraszanie ciepła: Smary rozpraszają ciepło powstające podczas obróbki, zapobiegając przegrzaniu krytycznych komponentów. Pomaga to zachować dokładność wymiarową i zmniejsza ryzyko rozszerzalności cieplnej.
- Gładka operacja: Właściwe smarowanie zapewnia płynniejsze i bardziej precyzyjne ruchy elementów maszyny. Jest to niezbędne do osiągnięcia wysokiej precyzji wymaganej w obróbce CNC.
- Zapobieganie korozji: Smary zapewniają barierę ochronną przed wilgocią i zanieczyszczeniami, zmniejszając ryzyko korozji powierzchni metalowych.
- Redukcja szumów: Smarowanie może zmniejszyć hałas generowany podczas pracy maszyny, tworząc cichsze i bardziej komfortowe środowisko pracy.
B. Punkty smarowania
Różne maszyny CNC mają różne punkty smarowania, które wymagają uwagi. Oto kilka typowych punktów smarowania, które należy wziąć pod uwagę:- Prowadnice liniowe: Nasmaruj prowadnice liniowe, co ułatwi ruch osi maszyny. Mogą to być śruby kulowe, łożyska liniowe i prowadnice.
- Łożyska wrzeciona: Nasmaruj łożyska wrzeciona, aby zapewnić płynny obrót i zmniejszyć tarcie podczas operacji cięcia lub obróbki.
- Mechanizm zmiany narzędzi: Jeśli Twoja maszyna jest wyposażona w automatyczny zmieniacz narzędzi, upewnij się, że ruchome części mechanizmu są odpowiednio nasmarowane, aby zapobiec zakleszczeniom lub awariom.
- Skrzynie biegów: Przekładnie, jeśli są obecne w Twojej maszynie, mogą wymagać smarowania w określonych odstępach czasu, aby utrzymać wydajność i zmniejszyć zużycie.
- Śruby kulowe: Śruby kulowe są kluczowymi elementami maszyn CNC. Prawidłowe smarowanie śrub kulowych i powiązanych z nimi elementów ma zasadnicze znaczenie dla dokładnego pozycjonowania i ruchu.
- Pompa płynu chłodzącego: Jeśli w Twojej maszynie zastosowano układ chłodzenia, upewnij się, że pompa jest odpowiednio nasmarowana oraz że płyn chłodzący jest czysty i wolny od zanieczyszczeń.
- Silniki osi: W zależności od typu silników używanych do ruchu osi (np. krokowy lub serwo), należy postępować zgodnie z zaleceniami producenta dotyczącymi smarowania i konserwacji.
- Uszczelki i uszczelki: W razie potrzeby sprawdź i wymień zużyte lub uszkodzone uszczelki i uszczelki, aby zapobiec wyciekom smaru i zanieczyszczeniu.
C. Harmonogram przeglądów
Ustanowienie harmonogramu regularnej konserwacji jest niezbędne, aby utrzymać maszynę CNC w optymalnym stanie. Oto kroki umożliwiające utworzenie harmonogramu konserwacji:Krok 1: Wytyczne producenta
Zapoznaj się z dokumentacją producenta i zaleceniami dotyczącymi częstotliwości konserwacji, rodzajów smarowania i konkretnych procedur.Krok 2: Codzienna konserwacja
Wdrażaj codzienne procedury konserwacji, które obejmują takie zadania, jak usuwanie zanieczyszczeń, sprawdzanie luźnych elementów złącznych i sprawdzanie poziomu płynu chłodzącego. Zadania te pomagają zapobiegać eskalacji drobnych problemów.Krok 3: Konserwacja cotygodniowa lub miesięczna
Zaplanuj bardziej szczegółowe zadania konserwacyjne co tydzień lub co miesiąc, w zależności od wykorzystania urządzenia. Może to obejmować dokładne czyszczenie, smarowanie i kontrolę najważniejszych komponentów.Krok 4: Konserwacja kwartalna lub półroczna
Wykonuj bardziej rozbudowane zadania konserwacyjne, takie jak sprawdzanie i regulacja osiowania, kontrola połączeń elektrycznych i wymiana zużytych lub uszkodzonych części.Krok 5: Coroczna konserwacja
Co roku należy rozważyć kompleksową kontrolę przeprowadzoną przez wykwalifikowanego technika lub inżyniera. Powinno to obejmować pełny cykl smarowania, kontrole kalibracji oraz wszelkie niezbędne naprawy lub wymiany.Krok 6: Dokumentacja
Prowadź szczegółową dokumentację wszystkich czynności konserwacyjnych, w tym daty, wykonane zadania i wszelkie zidentyfikowane problemy. Dokumentacja ta jest nieoceniona przy śledzeniu historii maszyny i planowaniu przyszłej konserwacji.Krok 7: Trening
Należy upewnić się, że personel odpowiedzialny za konserwację jest odpowiednio przeszkolony i ma dostęp do niezbędnych narzędzi i zasobów. Regularne smarowanie i konserwacja są niezbędne do maksymalizacji żywotności i wydajności maszyny CNC. Przestrzegając ustalonego harmonogramu konserwacji i dbając o punkty smarowania, możesz zapobiec przedwczesnemu zużyciu i mieć pewność, że Twoja maszyna będzie w dalszym ciągu produkować dokładne i wysokiej jakości detale. W następnym rozdziale omówimy procedury bezpieczeństwa i wytyczne dotyczące obsługi maszyny CNC.Rozdział 8: Procedury bezpieczeństwa dla maszyn CNC
Bezpieczeństwo jest sprawą najwyższej wagi podczas pracy z maszynami CNC. W tym rozdziale omówimy kluczowe procedury i wytyczne bezpieczeństwa dotyczące obsługi maszyn CNC, w tym bezpieczeństwo maszyn CNC, procedury wyłączania awaryjnego i stosowanie środków ochrony osobistej (PPE).A. Bezpieczeństwo maszyn CNC
- Dedykowane szkolenia: Upewnij się, że cały personel obsługujący maszyny CNC lub pracujący przy nich przeszedł kompleksowe szkolenie w zakresie bezpieczeństwa. Powinno to obejmować szkolenie dotyczące konkretnej maszyny, procedury bezpiecznej obsługi i rozpoznawanie zagrożeń.
- Strażnicy Maszyn: Utrzymuj wszystkie osłony maszyny i blokady zabezpieczające na swoim miejscu i sprawne. Te funkcje bezpieczeństwa mają na celu ochronę operatorów przed ruchomymi częściami i potencjalnymi zagrożeniami.
- Etykiety bezpieczeństwa: Upewnij się, że etykiety bezpieczeństwa i znaki ostrzegawcze są umieszczone w widocznym miejscu na maszynie. Etykiety te zawierają istotne informacje na temat potencjalnych zagrożeń i środków ostrożności.
- Awaryjny postój: Zapoznaj operatorów z lokalizacją i sposobem użycia przycisku zatrzymania awaryjnego. Upewnij się, że jest on łatwo dostępny w sytuacji awaryjnej.
- Wyczyść obszar roboczy: Utrzymuj wolną od bałaganu przestrzeń roboczą wokół maszyny CNC. Usuń wszelkie niepotrzebne narzędzia, materiały lub odpady, które mogą stwarzać ryzyko potknięcia się lub zakłócać działanie maszyny.
- Blokada/Oznakowanie maszyny (LOTO): Wdrożyć procedury blokowania/oznaczania w celu odłączenia zasilania i zabezpieczenia maszyny przed wykonaniem konserwacji lub naprawy. Urządzenia blokujące zapobiegają przypadkowemu uruchomieniu maszyny.
- Bezpieczeństwo wrzeciona i narzędzia: Ostrożnie obchodź się z narzędziami tnącymi i wymianą narzędzi. Należy upewnić się, że narzędzia są prawidłowo zamocowane w oprawkach narzędziowych i że zmiany narzędzi przeprowadzane są zgodnie z bezpiecznymi procedurami.
- Transport materiałów: Podczas przenoszenia ciężkich materiałów lub przedmiotów należy stosować odpowiedni sprzęt i techniki podnoszenia. Unikaj nadmiernego obciążania maszyny.
- Bezpieczeństwo przeciwpożarowe: Trzymaj w pobliżu gaśnice i czujniki dymu. Opracuj i przekaż protokoły bezpieczeństwa przeciwpożarowego, w tym lokalizację wyjść przeciwpożarowych i procedury ewakuacyjne.
B. Procedury awaryjnego wyłączania
- Przycisk zatrzymania awaryjnego: W sytuacji awaryjnej lub gdy wymagane jest natychmiastowe wyłączenie, naciśnij przycisk zatrzymania awaryjnego. Ten przycisk jest zazwyczaj duży, czerwony i łatwo dostępny.
- Zatrzymaj cały ruch: Przycisk zatrzymania awaryjnego powinien zatrzymać wszystkie ruchy maszyny i wyłączyć zasilanie maszyny. Upewnij się, że maszyna całkowicie się zatrzyma.
- Blokada/oznaczenie: Po użyciu przycisku zatrzymania awaryjnego należy postępować zgodnie z procedurami blokowania/oznaczania, aby zabezpieczyć maszynę i zapobiec przypadkowemu uruchomieniu.
- Powiadom władze: Jeśli zdarzy się wypadek lub niebezpieczna sytuacja, skontaktuj się z odpowiednimi władzami, takimi jak personel zajmujący się konserwacją lub przełożeni, aby rozwiązać problem i upewnić się, że maszynę można bezpiecznie ponownie obsługiwać.
C. Sprzęt ochrony osobistej (ŚOI)
- Okulary ochronne: Operatorzy i personel znajdujący się w pobliżu maszyny CNC powinni nosić okulary ochronne o odpowiedniej odporności na uderzenia, aby chronić oczy przed latającymi odłamkami.
- Ochrona słuchu: W hałaśliwych warsztatach mechanicznych należy nosić środki ochrony słuchu, takie jak zatyczki do uszu lub nauszniki, aby zapobiec uszkodzeniu słuchu.
- Rękawiczki: Podczas obchodzenia się z materiałami lub wykonywania czynności konserwacyjnych należy nosić rękawice odpowiednie do wykonywanej pracy. Należy upewnić się, że rękawice nie stwarzają zagrożenia w pobliżu ruchomych części maszyny.
- Ochrona dróg oddechowych: If materiał do obróbkiwytwarzają pył lub opary, należy stosować sprzęt ochrony dróg oddechowych, taki jak maski przeciwpyłowe lub maski oddechowe, aby zabezpieczyć się przed niebezpieczeństwem wdychania.
- Buty ochronne: Noś solidne obuwie ochronne lub buty z antypoślizgowymi podeszwami, aby chronić stopy przed urazami i zapewnić dobrą przyczepność w miejscu pracy.
- Odzież ochronna: W zależności od procesu obróbki i zastosowanych materiałów należy nosić odpowiednią odzież ochronną, taką jak fartuchy lub kombinezon zakrywający całe ciało.
- Kaski ochronne: W środowiskach, w których istnieje ryzyko spadających przedmiotów, należy nosić kaski ochronne lub twarde kapelusze w celu ochrony głowy.
- Osłony twarzy: W przypadku zadań, które wiążą się z potencjalnym zagrożeniem dla twarzy, takim jak rozpryskiwanie chłodziwa lub wiórów, oprócz okularów ochronnych należy używać osłon twarzy.
Rozdział 9: Rozwiązywanie typowych problemów instalacyjnych
W tym rozdziale przeanalizujemy typowe problemy, które mogą pojawić się podczas instalacji maszyn CNC i przedstawimy rozwiązania tych problemów. Ponadto omówimy techniki rozwiązywania problemów, które mogą pomóc w skutecznym identyfikowaniu i rozwiązywaniu problemów.A. Typowe problemy i rozwiązania
-
Problemy elektryczne:
- Problem: Maszyna CNC nie włącza się.
- Rozwiązanie: Sprawdź źródło zasilania, połączenia elektryczne i bezpieczniki. Upewnij się, że przycisk zatrzymania awaryjnego jest zwolniony.
-
Niewspółosiowość mechaniczna:
- Problem: Maszyna wykonuje niedokładne cięcia lub wymiary przedmiotu obrabianego.
- Rozwiązanie: Wyrównaj i wypoziomuj maszynę. Sprawdź, czy nie ma luźnych elementów lub zużytych prowadnic i wymień je w razie potrzeby.
-
Drganie lub wibracje narzędzia:
- Problem: Maszyna wytwarza wibracje lub drgania narzędzia, co wpływa na wykończenie powierzchni.
- Rozwiązanie: Sprawdź uchwyt narzędziowy i tuleję wrzeciona pod kątem prawidłowego osadzenia. Dostosuj parametry cięcia i ustawienia ścieżki narzędzia.
-
Błędy komunikacji:
- Problem: Sterownik CNC nie może komunikować się z komputerem ani oprogramowaniem CAD/CAM.
- Rozwiązanie: Sprawdź połączenia kablowe, szybkość transmisji i ustawienia zarówno na urządzeniu, jak i na komputerze. Zapewnij prawidłową instalację oprogramowania i sterowników.
-
Złamanie narzędzia:
- Problem: Narzędzia często pękają podczas obróbki.
- Rozwiązanie: Sprawdź wyrównanie narzędzia, stan oprawki narzędziowej i bicie wrzeciona. Dostosuj posuwy i prędkości w zależności od materiału narzędzia i przedmiotu obrabianego.
-
Problemy z chłodziwem lub smarowaniem:
- Problem: Niewystarczający lub nierówny przepływ chłodziwa/smaru.
- Rozwiązanie: Sprawdź elementy układu chłodzenia i smarowania, takie jak pompy, węże i dysze. Wyczyść lub wymień filtry i upewnij się, że poziom płynu jest prawidłowy.
-
Błędy oprogramowania:
- Problem: Oprogramowanie sterujące wyświetla komunikaty o błędach lub nieoczekiwane zachowanie.
- Rozwiązanie: Przejrzyj komunikaty o błędach i zapoznaj się z dokumentacją oprogramowania. Sprawdź problemy ze zgodnością i w razie potrzeby zaktualizuj oprogramowanie lub oprogramowanie sprzętowe.
B. Techniki rozwiązywania problemów
- Systematyczne podejście: Podczas rozwiązywania problemów należy przyjąć systematyczne podejście, identyfikując i izolując źródło problemu. Rozpocznij od najprostszych kontroli i stopniowo badaj bardziej złożone przyczyny.
- Dokumentacja: Wskazówki dotyczące rozwiązywania problemów i interpretacje kodów błędów można znaleźć w instrukcjach obsługi maszyny, dokumentacji i zasobach dostarczonych przez producenta.
- Pomiary i testowanie: Użyj przyrządów pomiarowych, takich jak czujniki zegarowe, suwmiarki i mikrometry, aby ocenić wyrównanie, wymiary i bicie narzędzia. Wykonaj cięcia testowe, aby sprawdzić dokładność obróbki.
- Oględziny: Przeprowadzić dokładną kontrolę wzrokową maszyny, sprawdzając, czy nie ma luźnych elementów złącznych, uszkodzonych elementów lub widocznych oznak zużycia.
- Dzienniki i zapisy: Przejrzyj dzienniki konserwacji, dzienniki błędów i zapisy przeszłych problemów, aby zidentyfikować powtarzające się problemy lub wzorce.
- Skonsultuj się z ekspertami: Jeśli napotkasz złożone lub uporczywe problemy, skonsultuj się z ekspertami, takimi jak pomoc techniczna producenta, wykwalifikowani technicy lub doświadczeni mechanicy, którzy mogli napotkać podobne problemy.
- Bezpieczne rozwiązywanie problemów: Zawsze dbaj o bezpieczeństwo podczas rozwiązywania problemów. Postępuj zgodnie z procedurami blokowania/oznaczania, wyłącz maszynę i używaj odpowiednich środków ochrony osobistej (PPE).
- Dokumentacja: Prowadź szczegółowe zapisy dotyczące działań związanych z rozwiązywaniem problemów, w tym podjętych kroków, obserwacji i zastosowanych rozwiązań. Zapisy te mogą być cenne do wykorzystania w przyszłości.
- Kontynuacja nauczania: Promuj kulturę ciągłego uczenia się i dzielenia się wiedzą w swoim zespole. Doświadczenie zdobyte podczas rozwiązywania problemów może prowadzić do ulepszonych praktyk konserwacji zapobiegawczej.
Rozdział 10: Końcowe kontrole i testowanie
W tym końcowym rozdziale omówimy podstawowe etapy uruchamiania programów testowych, zapewniania dokładności i dostrajania instalacji maszyny CNC w celu osiągnięcia optymalnej wydajności.A. Uruchamianie programów testowych
- Wybór programów testowych: Przygotuj programy testowe obejmujące szereg operacji obróbczych, które będzie wykonywać Twoja maszyna CNC. Programy te powinny obejmować podstawowe ruchy, zmiany narzędzi i różne scenariusze cięcia.
- Konfiguracja narzędzia i przedmiotu obrabianego: Zamontuj odpowiednie narzędzia i zabezpiecz obrabiany przedmiot na stole roboczym lub uchwycie maszyny. Upewnij się, że przesunięcia narzędzi i przesunięcia robocze są prawidłowo zaprogramowane.
- Próba: Na początek wykonaj pracę na sucho bez cięcia. Umożliwia to sprawdzenie ruchów maszyny, zmian narzędzi i ogólnego przebiegu programu pod kątem błędów lub nieoczekiwanego zachowania.
- Wybór materiału: Wybierz materiał testowy podobny do tego, którego planujesz użyć w swoich rzeczywistych projektach obróbki. Dzięki temu wyniki testów ściśle odzwierciedlają warunki rzeczywiste.
- Testy cięcia: Wykonaj programy testowe z operacjami cięcia. Monitoruj wydajność maszyny, zwracając szczególną uwagę na dokładność ścieżki narzędzia, prędkość wrzeciona i prędkości posuwu.
B. Zapewnienie dokładności
- Pomiar i kontrola: Po uruchomieniu programów testowych należy zmierzyć wymiary i wykończenie powierzchni detali testowych za pomocą precyzyjnych przyrządów pomiarowych. Porównaj wyniki z zamierzonymi specyfikacjami projektowymi.
- Kontrola narzędzia: Sprawdź narzędzia tnące pod kątem oznak zużycia, takich jak wyszczerbione krawędzie lub nadmierne zużycie narzędzi. W razie potrzeby wymień lub naostrz narzędzia.
- Kontrola przedmiotu obrabianego: Zbadaj przedmiot testowy pod kątem jakichkolwiek defektów, problemów z wykończeniem powierzchni lub odchyleń od pożądanej geometrii. Rozwiąż wszelkie problemy zidentyfikowane podczas inspekcji.
- Informacje zwrotne i analizy: Analizuj wyniki testów, aby zidentyfikować wszelkie rozbieżności lub odchylenia od oczekiwanych wyników. Określ, czy wymagane są korekty w celu poprawy dokładności.
C. Strojenie
- Optymalizacja ścieżki narzędzia: Jeśli wyniki testów wykażą niedokładności lub problemy z wykończeniem powierzchni, rozważ optymalizację ścieżek narzędzia w oprogramowaniu CAM. W razie potrzeby dostosuj parametry ścieżki narzędzia, wybór narzędzia oraz prędkości skrawania i posuwy.
- Regulacja parametrów maszyny: Zapoznaj się z dokumentacją maszyny, aby dostroić określone parametry, takie jak przyspieszanie, zwalnianie i kompensacja luzu. Te regulacje mogą zwiększyć dokładność.
- Kalibracja przesunięcia narzędzia: W razie potrzeby ponownie skalibruj przesunięcia narzędzi. Upewnij się, że maszyna dokładnie kompensuje długość i średnicę narzędzia, redukując błędy w obróbce.
- Korekta przesunięcia roboczego: Sprawdź i popraw przesunięcia robocze, aby mieć pewność, że maszyna pozycjonuje narzędzie dokładnie względem przedmiotu obrabianego. Małe błędy w przesunięciu punktu zerowego mogą prowadzić do znacznych niedokładności.
- Ponowne testowanie: Po dokonaniu regulacji i dostrojeniu należy ponownie uruchomić programy testowe, aby sprawdzić poprawę dokładności i wykończenia powierzchni.
- Dokumentacja: Dokumentuj wszystkie działania dostrajające, regulacje i wyniki testów do wykorzystania w przyszłości. Dokumentacja ta będzie cenna dla utrzymania spójności operacji obróbki.
Rozdział 11: Szkolenia i rozwój umiejętności
W tym rozdziale podkreślimy znaczenie szkoleń i rozwoju umiejętności zarówno dla operatorów maszyn, jak i personelu konserwacyjnego. Właściwe szkolenie i doskonalenie umiejętności mają kluczowe znaczenie dla zapewnienia bezpiecznej i wydajnej obsługi maszyny CNC, a także skutecznej konserwacji sprzętu i rozwiązywania problemów.A. Szkolenie operatorów
- Podstawowa obsługa maszyny: Operatorzy powinni przejść kompleksowe szkolenie w zakresie podstawowych aspektów obsługi maszyn CNC, w tym uruchamiania i wyłączania maszyny, powrotu do pozycji wyjściowej i impulsowania.
- Zrozumienie kodów G i kodów M: Operatorzy powinni być biegli w interpretowaniu i modyfikowaniu kodów G i M, które kontrolują ruchy i funkcje maszyny.
- Obsługa narzędzi: Właściwe techniki obsługi narzędzi, w tym wymiana narzędzi, przesunięcia narzędzi i kalibracja narzędzi, są niezbędne, aby zapobiec wypadkom i zapewnić dokładność obróbki.
- Konfiguracja przedmiotu obrabianego: Szkolenie powinno obejmować konfigurację przedmiotu obrabianego, w tym mocowanie przedmiotu obrabianego, ładowanie materiału i mocowanie przedmiotu obrabianego do stołu roboczego lub uchwytu maszyny.
- Procedury bezpieczeństwa: Operatorzy muszą być dobrze zaznajomieni z procedurami bezpieczeństwa maszyn CNC, protokołami wyłączania awaryjnego i stosowaniem środków ochrony osobistej (PPE).
- Podstawy rozwiązywania problemów: Podstawowe umiejętności rozwiązywania problemów, takie jak identyfikowanie typowych problemów i wiedza, kiedy szukać pomocy, mogą pomóc operatorom w szybkim rozwiązywaniu drobnych problemów.
- Kontrola jakości: Szkolenie w zakresie technik kontroli jakości i inspekcji jest niezbędne, aby mieć pewność, że gotowe detale spełniają określone tolerancje i wymagania dotyczące wykończenia powierzchni.
- Symulacja i praktyka: Operatorzy powinni mieć możliwość odbycia praktycznych ćwiczeń i ćwiczeń symulacyjnych, aby udoskonalić swoje umiejętności i zbudować pewność siebie w obsłudze maszyny CNC.
B. Szkolenie z konserwacji
- Konserwacja zapobiegawcza: Personel zajmujący się konserwacją powinien zostać przeszkolony w zakresie rutynowych zadań konserwacji zapobiegawczej specyficznych dla maszyny CNC, w tym procedur smarowania, czyszczenia i kontroli.
- Komponenty maszyny: Dogłębne zrozumienie komponentów maszyny, w tym silników, czujników, napędów i układów elektrycznych, jest niezbędne, aby personel konserwacyjny mógł skutecznie diagnozować i rozwiązywać problemy.
- Techniki rozwiązywania problemów: Zaawansowane umiejętności rozwiązywania problemów, takie jak diagnozowanie problemów elektrycznych, mechanicznych i związanych z oprogramowaniem, są niezbędne do minimalizacji przestojów i optymalizacji wydajności maszyny.
- Smarowanie i zarządzanie płynami: Właściwa wiedza na temat punktów smarowania, rodzajów płynów i systemów filtracji ma kluczowe znaczenie dla utrzymania integralności mechanicznej maszyny.
- Systemy elektryczne: Personel zajmujący się konserwacją powinien zostać przeszkolony w zakresie systemów elektrycznych, w tym w zakresie zrozumienia schematów okablowania, protokołów bezpieczeństwa elektrycznego i wymiany komponentów elektrycznych.
- Zaawansowana kalibracja: Szkolenia w zakresie zaawansowanych technik kalibracji, takich jak osiowanie laserowe i pomiar bicia wrzeciona, mogą poprawić dokładność maszyny CNC.
- Aktualizacje oprogramowania: Znajomość aktualizacji oprogramowania i aktualizacji oprogramowania sprzętowego jest ważna, aby oprogramowanie sterujące i oprogramowanie sprzętowe maszyny były aktualne.
C. Doskonalenie umiejętności
- Kontynuacja nauki: Promuj kulturę ciągłego uczenia się zarówno wśród operatorów, jak i personelu konserwacyjnego. Może to obejmować udział w warsztatach, seminariach i kursach online związanych z technologią CNC.
- Ocena umiejętności: Okresowo oceniaj umiejętności i wiedzę operatorów i personelu konserwacyjnego, aby zidentyfikować obszary wymagające poprawy i ukierunkowanego szkolenia.
- Trening obwodowy: Rozważ przeszkolenie operatorów w zakresie podstawowych zadań konserwacyjnych i odwrotnie. Może to poprawić ogólne zrozumienie i współpracę w zespole.
- Mentoring: Wdrażaj programy mentorskie, w ramach których doświadczeni pracownicy mogą udzielać wskazówek i dzielić się swoją wiedzą z mniej doświadczonymi członkami zespołu.
- Rozwiązywanie problemów: Zachęcaj pracowników do aktywnego angażowania się w ćwiczenia związane z rozwiązywaniem problemów i analizę przyczyn źródłowych, promując kulturę proaktywnego rozwiązywania problemów.
- Sprzężenie zwrotne: Ustanów pętlę informacji zwrotnej, w której operatorzy i personel konserwacyjny mogą zgłaszać problemy, dzielić się spostrzeżeniami i sugerować ulepszenia obsługi i konserwacji maszyn.
Wnioski
W tym obszernym przewodniku zbadaliśmy skomplikowany proces instalacji maszyny CNC, obejmując szeroki zakres tematów, aby mieć pewność, że maszyna CNC zostanie zmontowana, zainstalowana oraz będzie obsługiwana skutecznie i bezpiecznie. Podsumujmy kluczowe punkty, podkreślmy znaczenie prawidłowej instalacji maszyny CNC i spójrzmy w przyszłość technologii CNC.A. Podsumowanie kluczowych punktów
W całym tym przewodniku omówiliśmy następujące kluczowe punkty:- Zrozumienie maszyn CNC: Zaczęliśmy od omówienia, czym są maszyny CNC, różne dostępne typy i ich podstawowe komponenty.
- Przygotowanie przed instalacją: Podkreśliliśmy znaczenie przygotowania miejsca pracy, spełnienia wymagań dotyczących zasilania i elektryki oraz wdrożenia środków bezpieczeństwa przed instalacją.
- Montaż maszyny CNC: Podano szczegółowe kroki dotyczące rozpakowywania, organizowania komponentów, montażu ramy maszyny, mocowania silników i napędów, instalowania panelu sterowania i zarządzania kablami.
- Wyrównywanie i poziomowanie: Omówiliśmy znaczenie wyrównania i poziomowania, wymaganych narzędzi i krok po kroku proces osiągnięcia precyzyjnego wyrównania.
- Okablowanie elektryczne: Dokładnie omówiono zrozumienie układów elektrycznych, okablowanie maszyny CNC i przestrzeganie środków bezpieczeństwa podczas prac elektrycznych.
- Instalacja oprogramowania sterującego: Omówiono instalację oprogramowania sterującego, procedury kalibracji i testowania w celu zapewnienia prawidłowego działania maszyny CNC.
- Smarowanie i konserwacja: Podkreślono znaczenie smarowania i konserwacji dla trwałości i wydajności maszyny, łącznie z punktami smarowania i harmonogramami konserwacji.
- Procedury bezpieczeństwa: Aby stworzyć bezpieczne środowisko pracy, uwzględniono procedury bezpieczeństwa, protokoły wyłączeń awaryjnych i użycie środków ochrony osobistej (PPE).
- Rozwiązywanie typowych problemów z instalacją: Podano typowe problemy i techniki rozwiązywania problemów, aby pomóc w skutecznym identyfikowaniu i rozwiązywaniu problemów.
- Końcowe kontrole i testy: Omówiono uruchamianie programów testowych, zapewnienie dokładności i dostrajanie maszyny w celu osiągnięcia optymalnej wydajności.
- Szkolenie i rozwój umiejętności: Podkreślono znaczenie szkoleń operatorów i personelu konserwacyjnego oraz ciągłego podnoszenia kwalifikacji.
B. Znaczenie prawidłowej instalacji maszyny CNC
Właściwa instalacja maszyny CNC jest podstawą udanej operacji obróbki. Jest to istotne z następujących powodów:- Dokładność: Dobrze zainstalowana maszyna CNC z większym prawdopodobieństwem będzie wytwarzać dokładne i precyzyjne części, redukując ilość złomu i przeróbek.
- Bezpieczeństwo: Instalacja zgodna z normami i procedurami bezpieczeństwa zapewnia dobre samopoczucie operatorów maszyn i personelu konserwacyjnego.
- Długowieczność: Prawidłowa instalacja i regularna konserwacja przedłużają żywotność maszyny CNC, chroniąc Twoją inwestycję.
- Wydajność: Prawidłowo zainstalowana maszyna działa wydajnie, minimalizując przestoje i maksymalizując produktywność.
- Jakość: Jakość instalacji wpływa bezpośrednio na jakość obrabianych części, co prowadzi do zadowolenia klientów i lepszej reputacji.
C. Patrząc w przyszłość
W miarę ciągłego rozwoju technologii maszyny CNC staną się jeszcze bardziej wydajne i wszechstronne. Bardzo ważne jest, aby być na bieżąco z najnowszymi osiągnięciami, aktualizacjami oprogramowania i najlepszymi praktykami w obróbce CNC. Dodatkowo, w miarę jak technologia CNC staje się coraz bardziej dostępna, więcej branż i przedsiębiorstw może skorzystać z jej zalet. Podsumowując, instalacja maszyny CNC jest złożonym, ale satysfakcjonującym procesem. Postępując zgodnie ze wskazówkami i najlepszymi praktykami opisanymi w tym przewodniku, możesz przygotować grunt pod udaną operację obróbki CNC. Pamiętaj, że ciągłe uczenie się, szkolenia i ciągła konserwacja są kluczem do utrzymania i poprawy wydajności maszyn CNC, gdy patrzysz w przyszłość pełną możliwości w świecie produkcji precyzyjnej.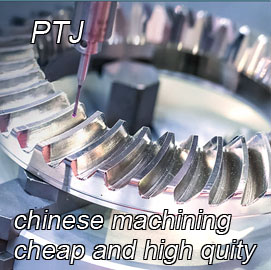
Usługi
- Obróbka 5-osiowa
- Frezowanie CNC
- Toczenie CNC
- Obróbka przemysłowa
- Proces obróbki
- Obróbka powierzchniowa
- Obróbka metali
- Obróbka tworzyw sztucznych
- Formy do metalurgii proszków
- Die Casting
- Galeria części
Case Studies
- Auto części metalowe
- Części maszynerii
- Radiator LED
- Części budowlane
- Części mobilne
- Części medyczne
- Części elektroniczne
- Obróbka na miarę
- Części rowerowe
Lista materiałów
- Obróbka aluminium
- Obróbka tytanu
- Obróbka stali nierdzewnej
- Obróbka miedzi
- Obróbka mosiądzu
- Obróbka super stopów
- Obróbka podglądowa
- Obróbka UHMW
- Jednolita obróbka
- Obróbka PA6
- Obróbka PPS
- Obróbka teflonowa
- Obróbka Inconelu
- Obróbka stali narzędziowej
- Więcej materiału
Galeria części